Jak przygotować maszynę na Przemysł 4.0?
Kontakt w sprawie artykułu: Wojciech Trojniar - 2018-04-05
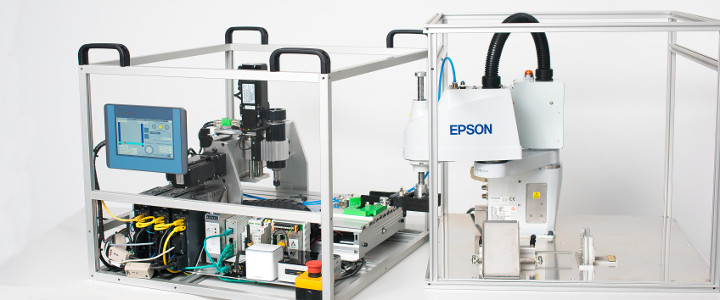
Z tego artykułu dowiesz się:
- Jakie produkty zostały wykorzystane podczas budowy frezarki Astraada CNC
- Jak przebiegał proces tworzenia projektu
- W jaki sposób działa program sterujący w tej aplikacji
Aby móc lepiej zrozumieć możliwości naszych produktów, postanowiliśmy wczuć się w rolę klientów, a dokładniej producentów maszyn i zbudować na bazie produktów z oferty ASTOR trójosiową frezarkę CNC.
Podczas budowy frezarki Astraada CNC użyliśmy następujących produktów:
- sterownik zintegrowany Astraada One z licencją CODESYS Softmotion CNC, EthernetIP i OPC UA,
- serwonapędy Astraada SRV 0.2 kW w wersji EtherCAT,
- miernik zużycia energii Comodis,
- switch Astraada NET i modem Astraada GSM,
- oprogramowanie InTouch Machine Edition,
- dostęp do chmury Wonderware InSight.
Urządzenie oprócz swojej podstawowej funkcjonalności miało wpisywać się w ideę Przemysłu 4.0, wymieniając informacje z poszczególnymi warstwami zarządzania produkcją i umożliwiając tworzenie spersonalizowanych wyrobów.
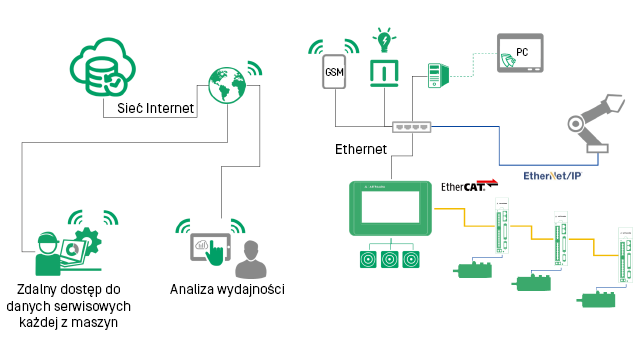
Naszym głównym celem była praktyczna weryfikacja funkcjonalności sprzętu i zastosowanie rozwiązań, które pozwoliłyby naszym klientom na budowanie innowacyjnych maszyn. Projekt prowadzony był pod kątem przygotowania wizualizacji i systemu sterowania serwonapędami, dlatego postanowiliśmy, że skorzystamy z gotowej mechaniki i na jej bazie powstanie obrabiarka. Taka decyzja pozwoliła oszczędzić mnóstwo czasu, który musiałby być poświęcony na projektowanie, zamawianie elementów, montaż itp.
Nie obyło się oczywiście bez modyfikacji, ale były to raczej niewielkie zmiany, przykładowo rozstaw otworów montażowych nie pasował do silników i musieliśmy przygotować odpowiednie przejściówki.
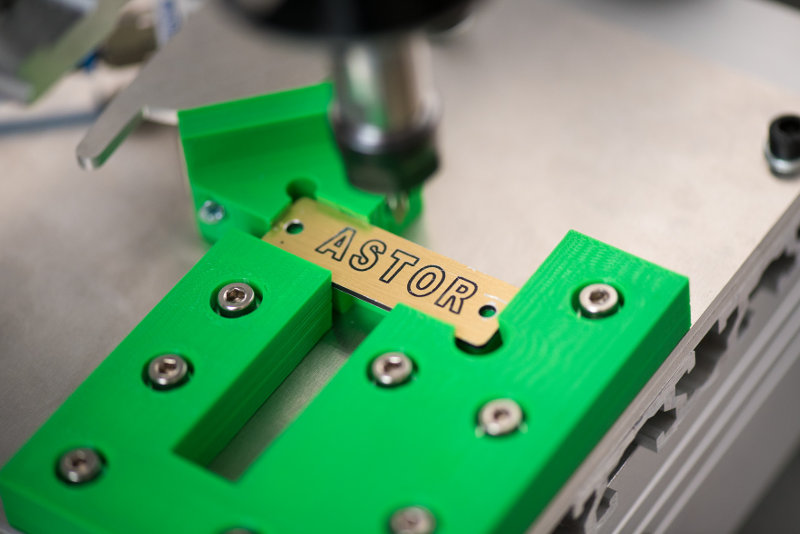
Frezarka została wyposażona w 6 krańcówek mechanicznych, które zabezpieczają maszynę przed błędami programistycznymi i niekontrolowanym ruchem poza fizyczny zakres poszczególnych osi. Wszystkie krańcówki podłączone są bezpośrednio do odpowiednich serwowzmacniaczy Astraada SRV i działają niezależnie od siebie, przez co są bardziej niezawodne. Mogą być aktywowane jedynie wtedy, gdy oś porusza się w odpowiednią stronę, np. dolny wyłącznik pionowej osi Z zatrzyma silnik napędzający śrubę jedynie wtedy, gdy wrzeciono będzie poruszać się w kierunku stołu obrabiarki.
200-watowe ekonomiczne serwosilniki Astraada SRV użyte do budowy frezarki posiadają enkodery absolutne, wraz z podtrzymaniem bateryjnym zamontowanym w okablowaniu pozwalają na zapamiętanie pozycji napędu nawet po odłączeniu zasilania. Takie rozwiązanie wyklucza konieczność czasochłonnego bazowania po każdorazowym odłączeniu prądu od frezarki. Jednak co jeśli trzeba będzie odpiąć silnik w celach serwisowych? Oczywiście w takim wypadku utracimy pozycję i trzeba będzie ponownie spozycjonować obrabiarkę. W tym celu na ramie obrabiarki zamontowane zostały 3 transoptory – każdy wpięty do oddzielnego serwowzmacniacza. Po aktywacji systemu bazowania każda z osi jedzie w odpowiednim kierunku. Gdy transoptor wykryje barierę – to znaczy, że każda z osi XYZ znalazła się w odpowiednim położeniu i jest to punkt startowy, dla którego należy przyjąć pozycję 0, 0, 0.
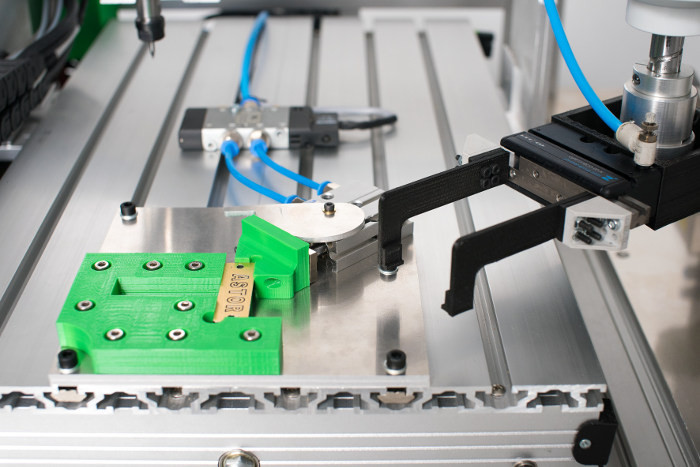
Do sterowania ruchem serwonapędów wykorzystany został zintegrowany 7” sterownik PLC Astraada One DC2007. Komunikuje się on z serwonapędami za pośrednictwem protokołu komunikacyjnego EtherCAT. Serwonapędowe wzmacniacze posiadają po dwa wbudowane porty (wejściowy i wyjściowy), więc do budowy sieci nie potrzeba dodatkowych switchy. Skuteczność działania EtherCAT potwierdzona jest świetnymi wynikami czasu wymiany informacji, umożliwiając sterowanie silnikami w „czasie rzeczywistym”. Jest to możliwe dzięki metodzie transmisji danych – ramka przesłana przez węzeł typu master przechodzi przez wszystkie węzły typu slave, które przetwarzają ją w locie. Informacja odbierana jest przez wszystkie węzły w sieci, gdzie każdy z nich najpierw sprawdza, czy znajdują się w nim dane bezpośrednio dla niego. Jeżeli tak, to odczytuje dedykowany fragment, a następnie wstawia swoją odpowiedź i przekazuje informację dalej. Gdy wiadomość dotrze do ostatniego urządzenia, ramka zostaje zawrócona do punktu wyjściowego.
Sterownik PLC Astraada One działa w środowisku Codesys dedykowanym dla producentów maszyn. Umożliwia ono przygotowanie logiki programu, wizualizacji, a także – dzięki licencji Softmotion CNC – synchronicznej pracy serwonapędów. W aplikacji sterującej użyliśmy wbudowanych w Codesysa bibliotek SM3.Basic i SM3.CNC. Aby móc z nich skorzystać na fizycznym sterowniku, należy kupić licencję Softmotion CNC lub zamówić bezpłatny plik z licencją demo. W przypadku, gdy korzystamy z wirtualnych osi, do testów spokojnie wystarczy wbudowany symulator.
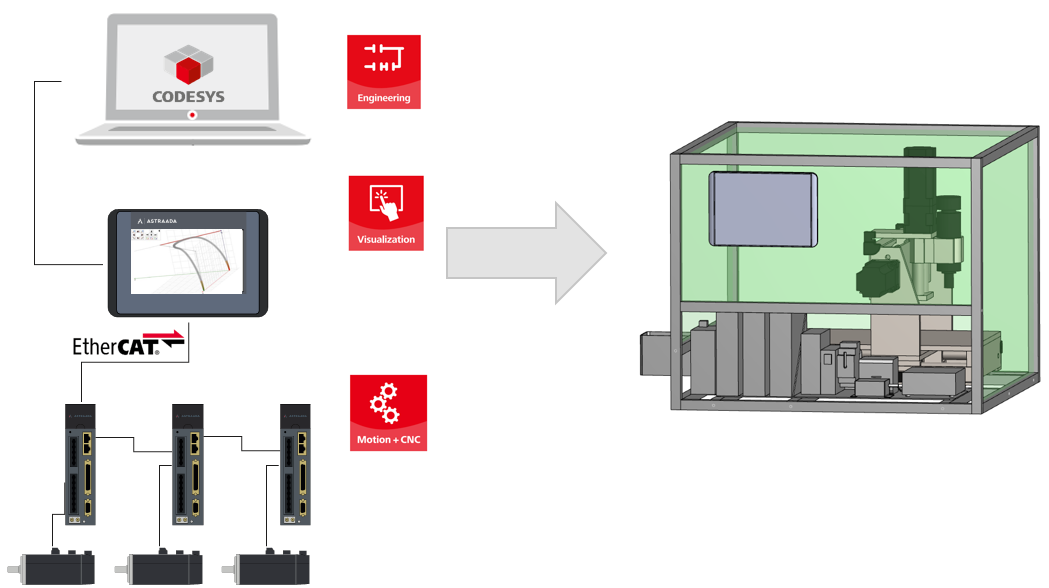
Działanie samego programu sterującego serwonapędami można podzielić na kilka głównych etapów:
- zezwolenie na załączenie poszczególnych osi obrabiarki,
- otwarcie programu G-Code z poziomu wbudowanego edytora lub skorzystanie z bloku funkcyjnego dekodera – jeśli korzystamy z zewnętrznego pliku .cnc,
- wygenerowanie trajektorii ruchu w układzie kartezjańskim – zamiany ciągłej ścieżki (programu G-Code) na dyskretną dzięki blokowi funkcyjnemu interpolatora,
- przeliczenie współrzędnych kartezjańskich z interpolatora na współrzędne osiowe zgodne z modelem kinematycznym frezarki,
- uruchomienie i kontrola ruchu jednoczesnej pracy trzech serwonapędów.
Wbudowany w Codesysa edytor G-Code dedykowany jest do tworzenia powtarzalnych programów nie wymagających zmian. W naszej aplikacji postanowiliśmy w nietypowy sposób wykorzystać tę funkcjonalność i użyć jej do grawerowania personalizowanych napisów. Do tego celu stworzyliśmy bazę liter zapisanych w G-Code. Użytkownik, wpisując np. imię i nazwisko z poziomu panelu sterownika, automatycznie generuje sekwencję grawerowania poszczególnych liter – tak, aby finalnie otrzymać żądany tekst (np. Jan Kowalski) na grawerowanym materiale.
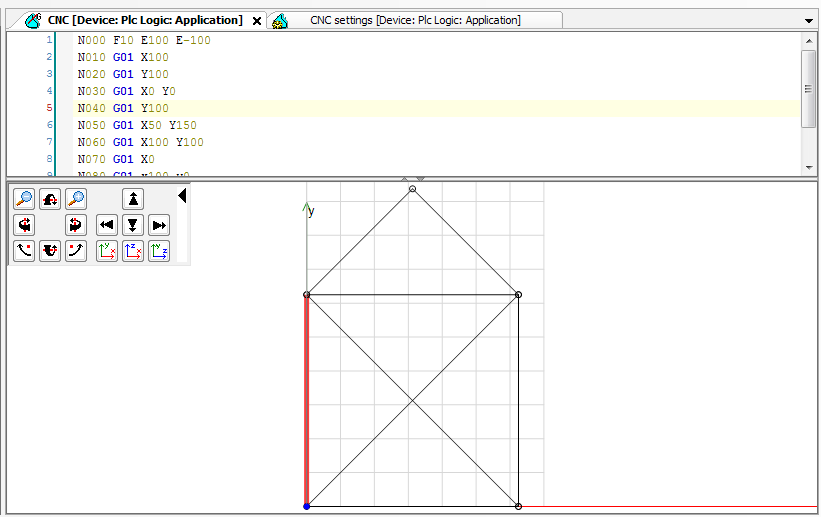
Tworzenie pliku .cnc z programem dla obrabiarki najczęściej jednak odbywa się z poziomu oprogramowania CAD/CAM, gdzie na bazie projektu detalu oraz wymiarów prefabrykatu generowana jest ścieżka G-Code. Tak przygotowany plik można wysłać do sterownika PLC Astraada One za pośrednictwem FTP. Po uruchomieniu programu obrabiarki, użytkownik na ekranie dotykowego panelu ma możliwość wyświetlenia aktualnej pozycji narzędzia skrawającego i wizualizację całego procesu obróbki. Pozwala to m.in. na wizualną kontrolę poprawności procesu skrawania.
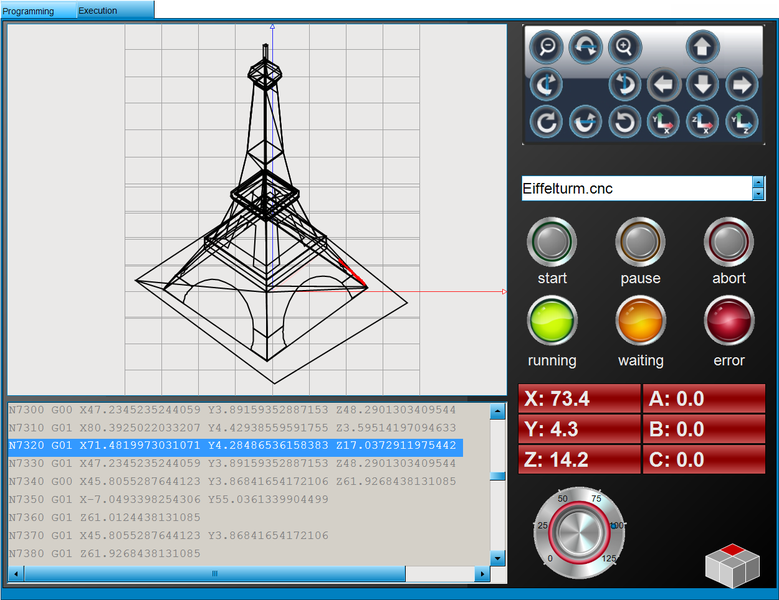
Zbudowana przez nas obrabiarka została wyposażona w bezprzewodowy system pomiaru energii Comodis. Zamontowany na przewodzie zasilającym przekładnik prądowy zbiera informacje o aktualnym poborze prądu i przesyła go do kontrolera komunikującego z się ze sterownikiem PLC Astraada One za pośrednictwem protokołu Modbus TCP. Takie rozwiązanie pozwala na połączenie w jeden system wielu rozproszonych mierników i zarządzanie nimi z poziomu wbudowanego interfejsu webowego. Zebrane informacje pozwalają m.in. na dokładne wyznaczenie kosztów związanych z obróbką pojedynczego detalu, uruchomienie trybu oszczędzania energii, a także detekcję usterek związanych ze zwiększonym zużyciem poboru prądu, takich jak np. zwiększone tarcie w łożyskach czy uszkodzenie silnika.
Przebieg wybranych zmiennych jak np. ilość wykonanych programów, czas pracy frezarki, dostępność czy zużycie energii można śledzić na wykresach w Wonderware InSight. Agregacja danych w chmurze Wonderware możliwa jest dzięki gateway’owi w postaci oprogramowania InTouch Machine Edition (ITME) zainstalowanemu na komputerze PC. ITME łączy się ze PLC Astraada One po dedykowanym protokole komunikacyjnym Codesys (COSYS) i przesyła co sekundę wybrane zmienne do chmury Wonderware. Webowy konfigurator umożliwia przygotowanie dowolnego raportu np. w postaci przebiegu zmiennej w czasie, krzywej narastającej czy wykresu Gantta.
Dodatkowo sterownik ma wgraną licencję OPC UA, co umożliwia zaciągnięcie danych bezpośrednio z PLC do systemu MES czy ERP np. w celu sprawdzenia wydajności pracy oraz zwrotne wprowadzanie zmian sterowania maszyną produkcyjną w oparciu o stany magazynowe półproduktów.
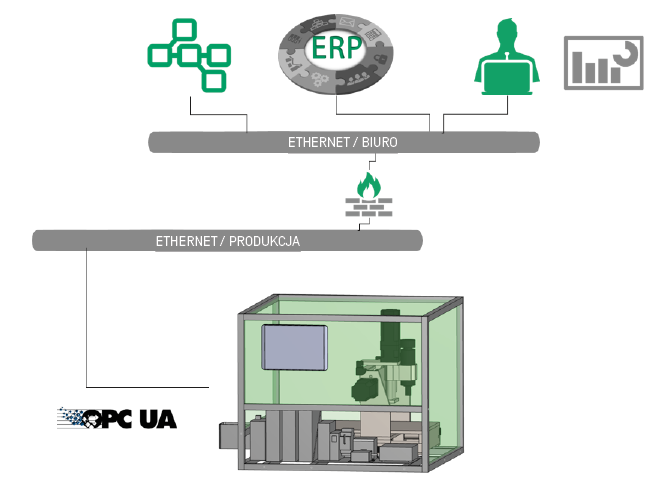
Aplikacja sterująca frezarką przygotowana jest w technologii Responsive Web Design (RWD). Powyższa funkcjonalność pozwoliła na stworzenie wizualizacji, idealnie dopasowanej do ekranów urządzeń mobilnych. RWD pozwoliło na przygotowanie dwóch wersji wizualizacji – dedykowanej na monitory o wysokiej rozdzielczości oraz urządzenia mobilne.
Jeśli jesteś producentem maszyn i szukasz rozwiązań, które pozwolą na podniesienie funkcjonalności Twoich produktów lub jesteś pracownikiem naukowym i szukasz stanowiska dydaktycznego dedykowanego do budowy i programowania maszyn, skontaktuj się z nami i umów na spotkanie, na którym będziemy mogli na żywo zaprezentować możliwości obrabiarki i szerzej omówić jej funkcjonalność. Do sprzętu udostępnimy Ci edytowalną wersję aplikacji, którą swobodnie można modyfikować i dopasować do indywidualnych potrzeb.
Do załadunku i rozładunku frezarki Astraada CNC wybrano robota Epson SCARA T3
Robot – jako gotowe urządzenie – został zamontowany, zaprogramowany do obsługi frezarki i uruchomiony w ciągu zaledwie kilku godzin. Jest to robot Epson SCARA o udźwigu 3 kg i zasięgu 400 mm. Robot T3 posiada zintegrowany kontroler, który komunikuje się ze sterownikiem Astraada za pomocą protokołu EtherNet/IP.
Zadaniem Epson T3 jest pobranie z magazynku nieobrobionego detalu spozycjonowanego za pomocą siłownika pneumatycznego. Do przenoszenia detalu wykorzystano pneumatyczny chwytak szczękowy o skoku 32 mm. Następnie nieobrobiony detal umieszczony zostaje w gnieździe w przestrzeni roboczej frezarki. Kolejny siłownik pneumatyczny pozycjonuje detal niwelując możliwość jego przemieszczenia się, wówczas robot opuszcza przestrzeń roboczą frezarki i wysyła sygnał zezwalający na proces obróbki.
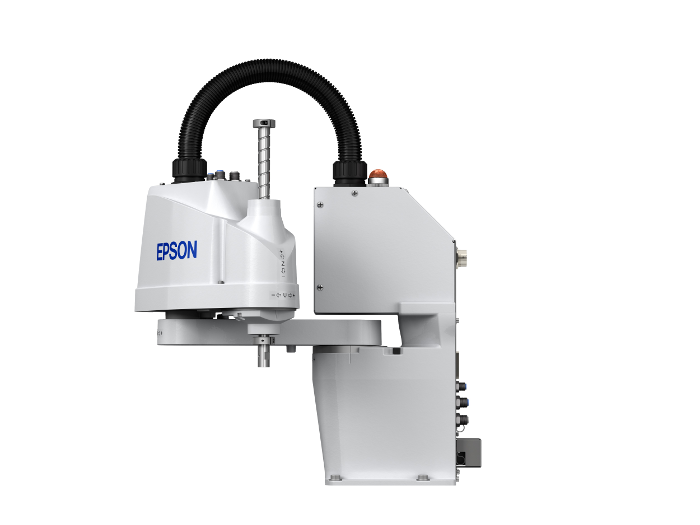
Wraz z zakończeniem grawerowania, wysyłany jest sygnał informujący o zwolnieniu detalu i zezwalający na ponowny wjazd robota w przestrzeń roboczą frezarki. Robot T3 chwyta detal, wyjmuje go z gniazda i przenosi go w miejsce odłożenia, skąd element transportowany jest w miejsce wydawania gotowego produktu – poza przestrzenią pracy robota.