4 powody, dla których warto standaryzować falownikowe układy napędowe
Kontakt w sprawie artykułu: Tomasz Kochanowski - 2020-03-18
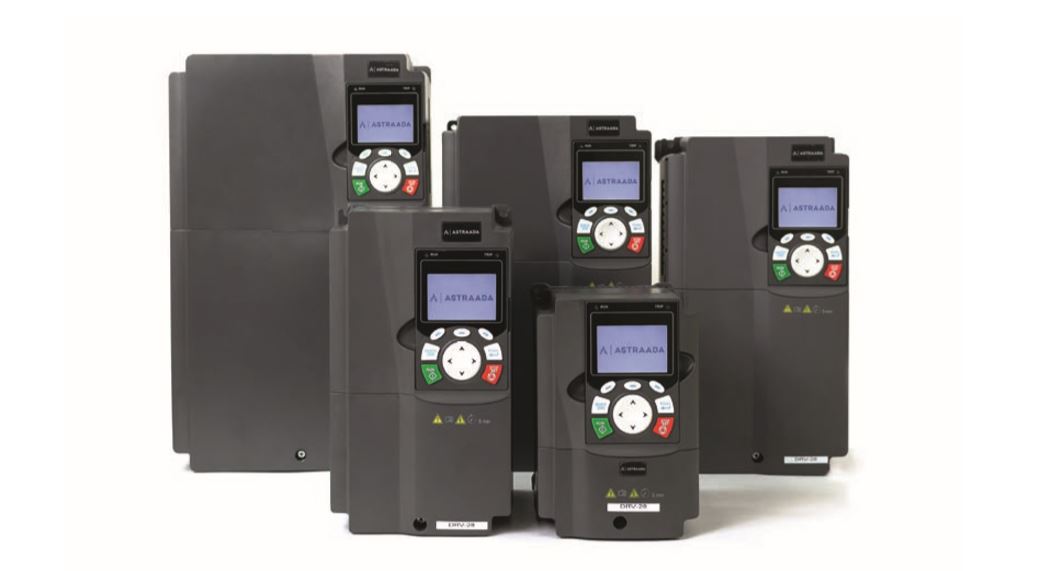
Z tego artykułu dowiesz się:
- Jak prawidłowo dobrać falownik do układu napędowego maszyny
- Jak zapewnić kompatybilność i zamienność falowników
- Jak uzyskać maksymalną funkcjonalność i użyteczność falownika
Stając przed doborem przemiennika częstotliwości do układu napędowego maszyny, poza podstawowymi pytaniami na temat napięcia zasilania, rodzaju obciążalności czy potrzebnej na montaż przestrzeni warto zadać sobie pytanie na temat możliwej standaryzacji falownikowych układów napędowych.
Co się kryje pod pojęciem standaryzacji? Pod pojęciem standaryzacji mam na myśli działanie polegające na analizowaniu wyrobu w celu zapewnienia:
- kompatybilności i zamienności,
- funkcjonalności i użyteczności,
- bezpieczeństwa i ergonomii użytkowania,
- ograniczenia zbędnej różnorodności.
Przy doborze przemienników częstotliwości do wyboru mamy serie dedykowane do konkretnych zastosowań np. falowniki do pomp i wentylatorów, falowniki do kompresorów, falowniki do suwnic i dźwigów lub wielofunkcyjne falowniki rozbudowywane o konkretne moduły rozszerzeń znacznie zwiększające ich zakres zastosowań.
To właśnie wykorzystanie modułowych urządzeń najmocniej wspiera standaryzację układów napędowych.
Poznajmy bliżej powody, dla których warto standaryzować falownikowe układy napędowe.
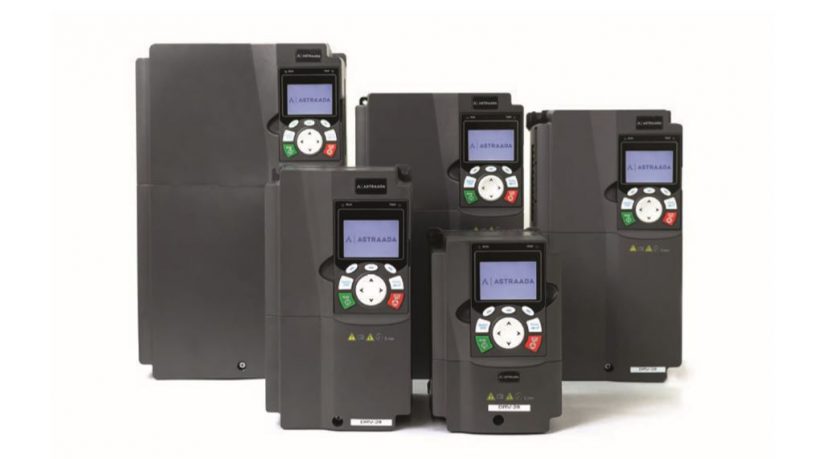
Po pierwsze: zapewnienie kompatybilności i zamienności
W przypadku falowników rozróżniamy modele w pierwszej kolejności po mocy wyjściowej (prądzie wyjściowym) i napięciu zasilającym – te parametry muszą być odpowiednio dobrane do aplikacji. Przestrzeń do standaryzacji otwiera się już przy doborze falownika do rodzaju podłączanego silnika.
Choć historia silnika elektrycznego liczy sobie ponad 170 lat, to wciąż jego konstrukcja ewoluuje. Związane jest to w dużej mierze z nowymi możliwościami przemienników częstotliwości w zakresie precyzyjnej regulacji prędkością i momentem oraz nieustanną potrzebą zwiększania efektywności energetycznej układu i zmniejszaniem jego gabarytów.
Obecnie w Polsce w automatyce wciąż najczęściej wykorzystywane są silniki asynchroniczne – w aplikacjach niewymagających precyzyjnego sterowania ruchem. Jednak w krajach Europy Zachodniej widać wyraźny wzrostowy trend zastosowań silników synchronicznych zapewniających lepszą dynamikę układu napędowego, większą dokładność, oraz – co staje się coraz bardziej istotne – znacznie większą sprawność silnika wpływającą na mniejsze zużycie energii elektrycznej, a co za tym idzie – poprawiającą efektywność energetyczną instalacji.
Planując nową inwestycję lub modernizując istniejący system, warto przy doborze falownika rozważyć urządzenie umożliwiające sterowanie zarówno silnikami asynchronicznymi, jak i synchronicznymi.
Przykładowo seria Astraada DRV-28 przystosowana jest do sterowania silnikami wysokoobrotowymi, serwosilnikami AC, silnikami synchronicznymi i asynchronicznymi. Posiada ona także wbudowane funkcje dedykowane do sterowania pracą elektrowrzeciona, wykorzystywanego w obrabiarkach sterowanych numerycznie czy centrach obróbczych CNC.
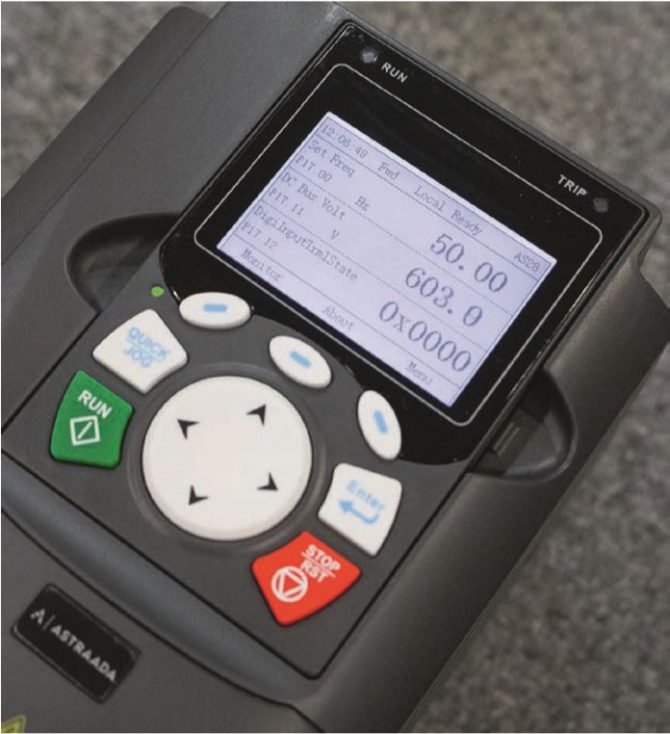
Po drugie: ograniczenie zbędnej różnorodności
Obciążenie obciążeniu nierówne – przekona się o tym zarówno strongman próbujący przebiec maraton, jak i ultramaratończyk próbujący swych sił w martwym ciągu. Tak jak sportowcy odpowiednio dobierają program ćwiczeń do pokonania stawianych sobie wyzwań, tak samo automatyk – dobierając falownik powinien wybrać odpowiedni model dostosowany do charakteru obciążenia i typu rozruchu. Tu z pomocą przychodzą niektórzy producenci falowników dostarczający modułowe urządzenia znacznie rozszerzające ich zakres zastosowań.
To właśnie od rodzaju obciążenia uzależniony będzie dobór falownika pod kątem metody sterowania, typu rozruchu, pracy stało- lub zmienno-momentowej. Przy stosowaniu falownika do napędów „lekkich” – takich jak pompy, wentylatory, sprężarki, przenośniki – wystarczające są zazwyczaj falowniki ze sterowaniem skalarnym (U/f).
Do aplikacji napędowych wymagających większego momentu rozruchowego i dużej przeciążalności – takich jak napędy maszyn, obrotnice, wirówki – najlepiej sprawdzają się falowniki z bezczujnikowym sterowaniem wektorowym (SVC). Posiadają one możliwość automatycznego pomiaru parametrów silnika i – na jego bazie – optymalnego dopasowania parametrów przemiennika do podłączonego układu napędowego.
Do najbardziej zaawansowanych aplikacji wymagających wysokiej precyzji w kontroli prędkości i momentu przy zmiennych warunkach obciążenia, zalecane jest stosowanie falowników przystosowanych do podpięcia sygnału z enkodera, a co za tym idzie – sterowania dynamicznym wektorem strumienia pola (VC). Ze względu na różne typy enkoderów, do ich podpięcia wykorzystuje się dedykowane moduły rozszerzeń – przykładowo seria DRV-28 posiada 3 różne moduły enkoderowe.
Po trzecie: zapewnienie funkcjonalności i użyteczności.
Przemienniki częstotliwości mogą pracować jako niezależne, lokalne układy napędowe lub jako elementy większego, rozproszonego systemu sterowania. W przypadku tych pierwszych istotna będzie odpowiednia ilość wejść / wyjść wykorzystywana do zadawania częstotliwości, uruchamiania i zatrzymywania napędu oraz ewentualnego alarmowania o zaistniałym problemie.
W takich systemach funkcje sterowania całym układem może realizować zewnętrzny, niezależny sterownik PLC lub sterownik PLC montowany w falowniku jako opcjonalna karta rozszerzeń. To drugie rozwiązanie dostępne jest w falownikach Astraada DRV-28 i umożliwia wykorzystanie prostego systemu sterowania.
Dla falowników pracujących w rozproszonych systemach sterowania, istotne są możliwości komunikacyjne pozwalające na połączenie układu napędowego z centralnym systemem sterowania. W najprostszych systemach wystarczająco może być komunikacja po wbudowanym porcie RS-485, obsługującym protokół Modbus RTU, umożliwiając sterowanie silnikiem oraz monitorowanie i korektę parametrów pracy.
Obecnie jednak ze względu na ilość wymienianych danych, wygodę stosowania sieci Ethernet i rozbudowane funkcje diagnostyczne, znacznie powszechniejsze staje się wykorzystanie opcjonalnych kart komunikacyjnych do sieci Profinet czy EtherCAT.
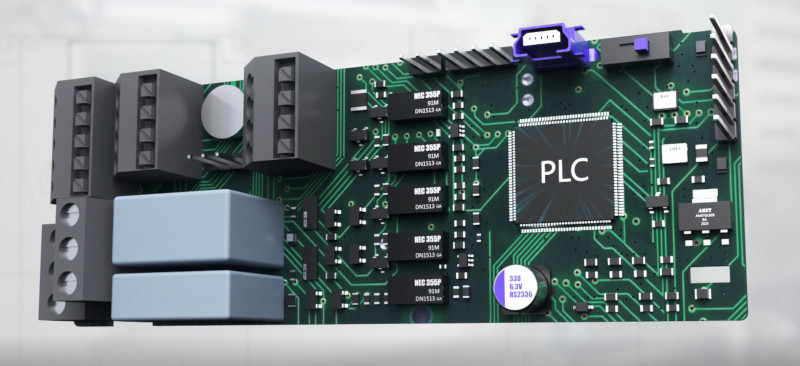
Po czwarte: bezpieczeństwo i ergonomia użytkowania.
Z kolei przy eksploatacji układu napędowego istotna jest możliwość szybkiej detekcji problemu i ewentualnej podmiany urządzenia w przypadku jego uszkodzenia, ograniczająca do minimum czas przestoju instalacji. Im większa standaryzacja urządzeń, tym łatwiej utrzymać racjonalny magazyn serwisowy zapewniający ciągłość pracy w zakładzie.
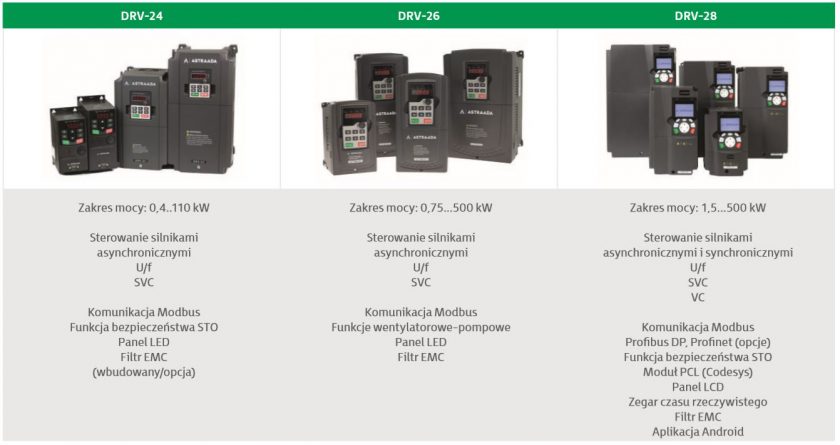
Monitorowanie statusu rozproszonego układu napędowego możliwe jest zazwyczaj za pomocą sieci komunikacyjnej np. Profinet, niemniej w przypadku niezależnej maszyny lub wystąpienia nieprawidłowości w pracy układu sieciowego, istotna w eksploatacji staje się szybka diagnostyka z poziomu konkretnego przemiennika częstotliwości.
W tym celu z pomocą przychodzą aplikacje na urządzenia mobilne i funkcjonalne panele sterowania z wyświetlaczami LCD. Z poziomu lokalnego panelu LCD można nie tylko szybko skonfigurować urządzenie, monitorować jego bieżące parametry pracy, czy odczytać informacje o czasie i przyczynie wystąpienia błędu, ale również szybko przenieść konfigurację pomiędzy urządzaniami. Przy projektowaniu układu napędowego maszyny czy linii technologicznej równie istotne jest spełnienie bieżących wymagań, co możliwość jego rozbudowy w przyszłości. Stosowanie standaryzacji układów napędowych znacząco upraszcza proces tworzenia i modernizacji instalacji.
[[sklep 136]]