Treści
Elastyczne sposoby korzystania z oprogramowania przemysłowego
Elastyczne sposoby korzystania z oprogramowania przemysłowego
Nie trzeba już posiadać nowoczesnych rozwiązań technicznych by móc z nich korzystać. Bardziej innowacyjny i efektywniejszy kosztowo jest model subskrypcyjny. Nowy trend obniża próg wejścia, zapewnia większą elastyczność i podnosi poziom cyberbezpieczeństwa, jeśli chodzi o korzystanie z nowych technologii.
Podejście do posiadania w ostatnich czasach uległo gruntownej zmianie. Klienci indywidualni nie kupują już filmów, muzyki, audiobooków czy gier na płytach. Coraz częściej korzystają ze streamingu, a gry i książki pobierają z sieci. Decydują się też na carsharing zamiast posiadania własnych samochodów. Zmiana widoczna jest także w biznesie. Firmy nie kupują pakietów biurowych czy oprogramowania do projektowania graficznego, a raczej decydują się na model subskrypcyjny. Coraz częściej dotyczy to także rozwiązań stosowanych w branży produkcyjnej.
Ta zmiana wiąże się między innymi z popularyzacją myślenia i działania w paradygmacie czwartej rewolucji przemysłowej, a więc organizowania środowiska produkcyjnego z wykorzystaniem najnowszych osiągnięć technologicznych (AI, IIoT, BigData) oraz innowacyjnego podejścia biznesowego. Przemysł 4.0, stawia na intensywne zmiany. Jednym z jego filarów jest orientacja na usługi, a więc podejście, które zakłada, że aby używać produkt, nie koniecznie musimy go posiadać. Ważniejszy jest dostęp do niego na pożądanych warunkach. Takie podejście ma dwa wymiary. Z jednej strony producentom łatwiej docierać do klientów, gdy można zaoferować im model subskrypcyjny, ale z drugiej strony sami producenci mogą skorzystać z takiego modelu by zoptymalizować proces produkcji.
Nie oznacza to, że model subskrypcyjny jest już dominujący, ani że można całkowicie obyć się bez posiadania. Niektóre narzędzia warto po prostu mieć na własność. Rośnie jednak zakres produktów z obszaru oprogramowania, których posiadanie nie jest koniecznością, a wręcz model subskrypcyjny jest w ich przypadku dużo bardziej efektywny. Dlaczego?
Pierwszy z powodów jest taki, że w warunkach szybkiego postępu technologicznego sytuacja, w której pewne rozwiązanie będzie spełniało swoją funkcję przez lata, bez konieczności modyfikowania go, jest coraz mniej realna. W świecie oprogramowania ta ewolucja poszczególnych systemów przyspiesza. Nie inaczej jest w obszarze oprogramowania przemysłowego. Raz zakupione oprogramowanie trzeba modyfikować, co oznacza dodatkowe koszty. Zarówno w branży IT (Information Technology), jak i branży OT (Operational Technology) cykl życia produktu technologicznego znacząco się skrócił. Założenie, że można zainwestować w sprzęt czy oprogramowanie i przez pięć czy dziesięć lat nic nie modyfikować, jest obecnie złudne. Nie wynika to wyłącznie z dynamiki postępu technologicznego, ale także ze specyfiki współczesnego otoczenia biznesowego, a także kwestii cyberbezpieczeństwa.
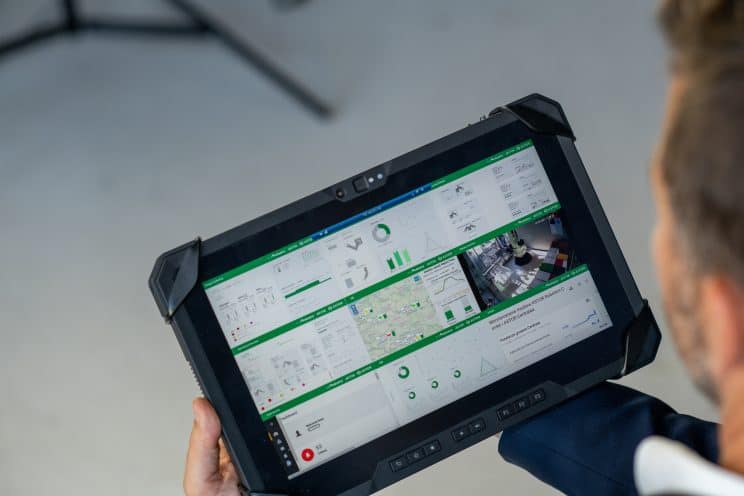
Obecnie rynki zmieniają się dużo szybciej niż jeszcze kilka lat temu. To efekt sytuacji geopolitycznej (wojna w Ukrainie), zerwanych łańcuchów dostaw jeszcze w wyniku pandemii, ale też z rosnącej świadomości klientów, pewnych trendów demograficznych takich jak wchodzenie na rynek pokoleń zorientowanych na szybkie zmiany i cyfrowy dostęp do produktów. Wszystkie te zjawiska wymuszają na biznesie, w tym biznesie produkcyjnym, działanie w trybie dużo bardziej elastycznym, zwinnym niż dotąd.
W obszarze IT, zwinne prowadzenie projektów jest powszechne. Jednak we współczesnym środowisku produkcyjnym takie podejście wciąż ma pole do rozwoju. Coraz częściej, zwinne prowadzenie projektów produkcyjnych staje się koniecznością, gdy zmieniają się potrzeby klientów, gdy pojawia się konieczność stworzenia spersonalizowanej partii produktów, gdy pojawiają się kłopoty z surowcami czy półproduktami i wymagane jest szybkie przezbrojenie linii produkcyjnej. Przy zwinnym podejściu zakup jednego rozwiązania na lata się nie sprawdza. Bardziej praktyczny staje się model dzierżawy. Przemawia za nim fakt, że rozwiązania, które w ramach abonamentu otrzymuje klient, mają strukturę modułową, dzięki czemu można je uzupełniać o nowe funkcjonalności, na przykład chmurowe.
Dlaczego funkcjonalności chmurowe są tak ważne w kontekście przemysłowym? Rozwiązania tego typu same mają strukturę modułową, co oznacza, że można je szybko rozbudowywać i ograniczać ich zasięg. W środowisku produkcyjnym oznacza to, że można mieć dostęp do pewnych funkcji, np. analitycznych bez konieczności inwestowania we własną infrastrukturę, czy to w jej zakup, czy później w utrzymanie. Jeśli chcemy przetwarzać duże zbiory danych i analizować je np. z wykorzystaniem sztucznej inteligencji, chmura to ułatwia. Kiedy funkcje te przestają być potrzebne, nie trzeba mierzyć się z problemem niepotrzebnej infrastruktury.
Chmura zapewnia też mobilność, bo rozwiązanie to gwarantuje bezpieczny dostęp do danych z dowolnego urządzenia, w dowolnym czasie. Sprawia, że proces produkcji można obserwować zdalnie i interweniować, gdy tylko pojawią się jakieś anomalie.
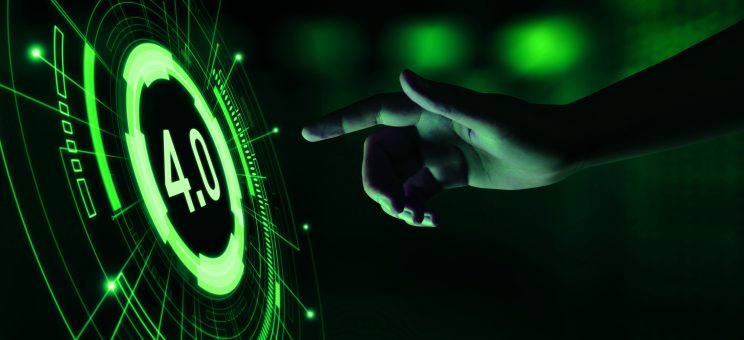
Systemy hybrydowe
Choć technologie chmurowe są silnie związane z modelem subskrypcyjnym czy abonamentowym, zakłady przemysłowe nie są na nie skazane, gdy zdecydują się na abonament. Dostępne i niekiedy bardzo przydatne są także rozwiązania hybrydowe.
Z punktu widzenia firm, które korzystają z oprogramowania przemysłowego, takie hybrydowe podejście jest szczególnie atrakcyjne. Daje możliwość odcięcia od Internetu, tych części systemu, które mają znaczenie krytyczne, a jednocześnie rozbudowywania go o nowe funkcjonalności dzięki rozwiązaniom chmurowym, które z Internetu korzystają. Szczególną korzyść dla zakładów przemysłowych może przynieść takie wykorzystanie chmury, które pozwala na używanie sztucznej inteligencji, na przykład do przewidywania zdarzeń niepożądanych, takich jak awarie czy przestoje, na długo przed ich wystąpieniem, tak aby móc im zapobiegać, a tym samym unikać kosztownych napraw.
Obszarem, w którym wykorzystanie rozwiązań chmurowych i sztucznej inteligencji może przynosić również duże korzyści, jest predykcja zapotrzebowania na zużycie mediów produkcyjnych. To ostatnio temat szczególnie gorący ze względu na rosnące ceny prądu i gazu oraz innych surowców. Oszczędności, które można poczynić uszczelniając proces i zapobiegając wyciekowi energii z powodów, które trudno dostrzec, byłyby w firmach produkcyjnych szczególnie pożądane. Sztuczna inteligencja może analizować dane historyczne dotyczące procesu produkcyjnego i na ich postawie przewidywać optymalizacje linii produkcyjnej w taki sposób, by zużycie energii i koszty z nim związane minimalizować.
Elastyczność AVEVA Flex
Okazuje się jednak, że wcale nie trzeba decydować się na rozwiązania chmurowe, ani nawet hybrydowe, by w sposób elastyczny korzystać z nowoczesnego oprogramowania w środowisku produkcyjnym i w sposób płynny dostosowywać pracę zakładu produkcyjnego do potrzeb rynku. Można postawić na rozwiązania instalowane on premise, ale takie, które w ramach jednego abonamentu dają możliwość ciągłej modyfikacji funkcji. Przykładem jest AVEVA Flex.
Jest to licencyjny model korzystania z oprogramowania, który niesie dwie zasadnicze korzyści. Po pierwsze pozwala elastycznie dostosowywać oprogramowanie do wymogów produkcji, po drugie znacząco obniża próg wejścia, w kontekście korzystania z nowych rozwiązań.
Licencja AVEVA Flex zawierana jest na pewien okres, na przykład trzy czy pięć lat i przez ten czas, użytkownik może wprowadzać pewną liczbę modyfikacji komponentów systemu, w zależności od swoich potrzeb. Nie musi kupować nowych modułów za każdym razem. Jego umowa licencyjna zapewnia mu możliwość dokonywania licznych zmian.
System ułatwia wdrażanie nowych pomysłów dotyczących modyfikacji linii produkcyjnej. Dzięki elastycznej modyfikacji oprogramowania możliwe jest szybkie stworzenie tzw. proof of concept, czyli przetestowanie pewnej hipotezy i jeśli okaże się ona obiecująca szybka implementacja.
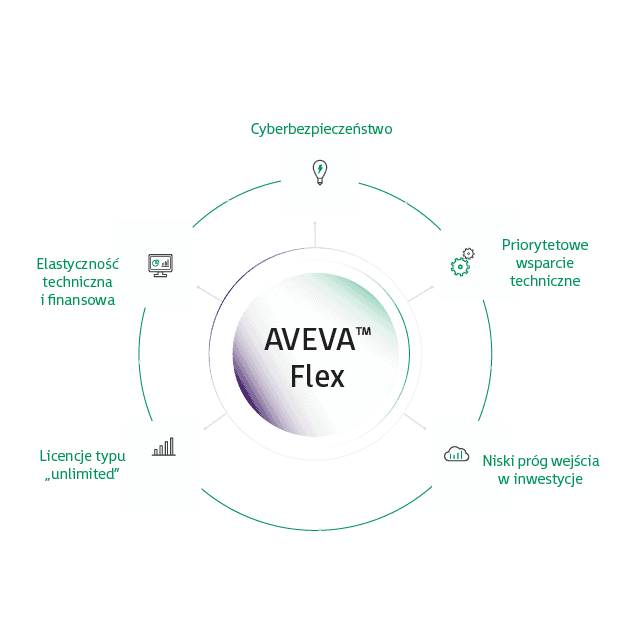
Firma AEVA, będąca jednym z największych producentów oprogramowania przemysłowego na świecie, przeprowadziła badania pokazujące, jak firmy użytkują taki software w początkowej fazie. Okazuje się, że w 85% firm produkcyjnych wdrożenie pilotażowe trwa dłużej niż rok, czyli naprawdę długo. Jednocześnie ok. 70% firm produkcyjnych oczekuje, że po roku nastąpi zwrot z inwestycji w oprogramowanie. Trudno pogodzić te sprzeczne oczekiwania. Pierwszy rok pilotażu musi przecież upłynąć pod znakiem testowania hipotez dotyczących optymalnych modeli operacyjnych, wymaga pewnych nakładów inwestycyjnych. W rezultacie nie starcza czasu na to, by inwestycja mogła się zwrócić.
Sposobem na pokonanie tych trudności może być model subskrypcyjny, który znacząco skraca czas potrzebny na uruchomienie poszczególnych rozwiązań, gwarantując dużą elastyczność działania. Po pierwsze można szybko uruchomić oprogramowanie nie w wersji demonstracyjnej, a w pełnej. Po drugie, w ramach jednej licencji można dokonywać modyfikacji pakietu oprogramowania, jeśli w trakcie programu pilotażowego okaże się, że pewne funkcjonalności można, albo trzeba zmienić.
Co więcej w ramach systemu można także w sposób elastyczny zarządzać licencjami dla osób korzystających z systemu. W początkowej fazie może być potrzebna większa liczba licencji deweloperskich, a gdy system jest już w pełni funkcjonalny, można przerzucić się na zwykłe licencje dostępowe. System daje też dostęp do najnowszych wersji oprogramowania. Nie ma konieczności ich instalowania, ale jeśli klient chce zaktualizować system, może to zrobić w ramach licencji. Elastyczność systemu wiąże się z możliwością korzystania z pełnego wsparcia technicznego, zapewniającego nie tylko doradztwo techniczne, ale też wsparcie w zakresie cyberbezpieczeństwa.
Niski próg wejścia
Poza wymiarem funkcjonalnym, jest jeszcze wymiar ekonomiczny. Próg wejścia, jeśli chodzi o rozwiązania typu AVEVA Flex jest zdecydowanie niższy niż w przypadku tradycyjnych licencji wieczystych. Za abonament AVEVA Flex trzeba zapłacić zaledwie 30% wartości licencji wieczystej. To koszty nabycia rozwiązania, ale jest jeszcze jeden parametr, który należy wziąć pod uwagę: całkowity koszt użytkowania (Total Cost of Ownership, TCO). Tu także, dzięki elastycznemu podejściu do funkcji i możliwości dostosowania ich do potrzeb, model abonamentowy wygrywa z modelem licencji wieczystej.
Zdecydowanie niższa cena, niższe ryzyko związane z testowaniem nowych rozwiązań, przy pełnym wsparciu serwisowym oznaczającym między innymi możliwość stałej aktualizacji oprogramowani i duża elastyczność, jeśli chodzi o ewentualne zmiany konfiguracji systemu – wszystkie te cechy systemu abonamentowego, takiego jak AVEVA Flex, sprawiają, że staje się on niezwykle atrakcyjny we współczesnych zakładach produkcyjnych, które w warunkach niepewności rynkowej i w obliczu czwartej rewolucji przemysłowej chcą zdobywać przewagę konkurencyjną.