4 Archetypy fabryk przyszłości
Przemysł 4.0 zaistniał już w świadomości polskich inżynierów i menedżerów. Badania prowadzone wśród inżynierów pokazują, że w stosunku do roku 2016 potrafimy bardzo precyzyjnie określić, w której rewolucji znajdują się nasze firmy. Około 80% jednoznacznie wskazuje, że rozpoczynają lub przechodzą 3. rewolucję.
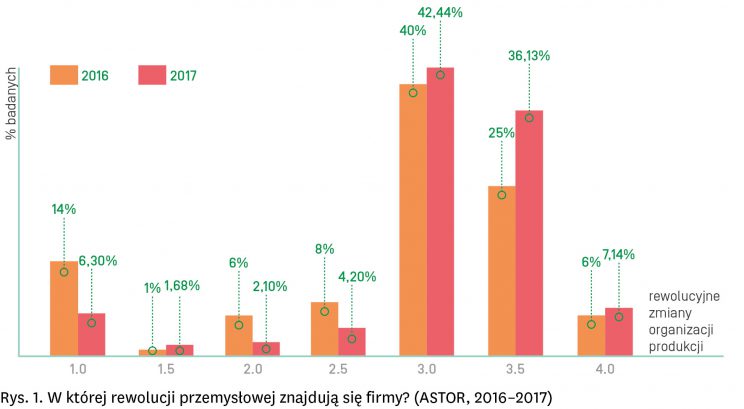
Kluczowe pytanie zadawane przez menedżerów w ostatnim półroczu brzmi: Co dla mnie oznacza nadejście Przemysłu 4.0? Jeżeli firma, którą zarządzasz, realizuje tylko produkcję (czyli środkowy etap łańcucha wartości), to po pierwsze, na pewno odczuwasz presję na obniżenie ceny jednostkowej produktu. Po drugie, prawdopodobnie marża, którą wypracowujesz jest niższa od oczekiwań. Po trzecie, patrząc na dynamicznie zmieniający się rynek pracy i brak pracowników, w najbliższym czasie możesz mieć poważne problemy z zapewnieniem zdolności produkcyjnych. Jakie są zatem możliwe scenariusze rozwoju fabryk?
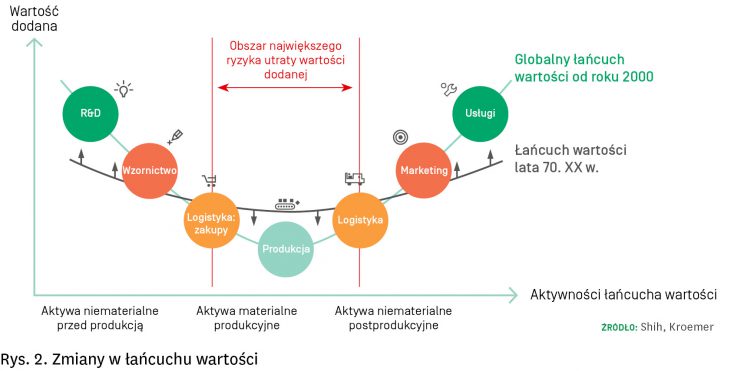
Wynika to m.in. z tego, że koszty dostępu do technologii (np. robotyzacji) znacząco spadły, ale główną motywacją do ich wprowadzania jest presja na obniżanie ceny i brak pracowników. Odczuwalny jest także spadek konkurencyjności firm, które oparły swoją strategię tylko na obszarze Produkcji (por. rys. 2), dodatkowo opierając się na sieciach dyskontowych jako głównym kliencie. Budujące jest to, że na rynku można spotkać firmy, które rozwijają bardziej wartościowe elementy łańcucha wartości, np. R&D (ang. Research and Development, Badania i Rozwój), tworzenie marek własnych, czy rozwijanie zdolności logistyczno-dystrybucyjnych. Warto wspomnieć, że te zmiany w łańcuchu wartości działają w skali globalnej. Oznacza to, że firma produkcyjna ulokowana w Szwecji, dzięki automatyzacji i cyfryzacji jest w stanie osiągnąć dziś podobny poziom kosztów produkcji jak jej polski odpowiednik. Dodatkową presją rynkową jest powszechne oczekiwanie klientów, że ich produkt będzie spersonalizowany.W tej sytuacji potrzebna jest strategiczna decyzja: w którym kierunku rozwijać fabryki?
Rola klienta w życiu fabryki
Pierwszym i podstawowym czynnikiem determinującym przyszły obraz twoich fabryk będzie charakterystyka twojego klienta i jego oczekiwań względem produktów. Proces analizy potrzeb i oczekiwań klientów warto przeprowadzić z dwóch perspektyw: zewnętrznej i wewnętrznej. Z perspektywy zewnętrznej można wykorzystać do tego narzędzia takie jak:
- Value Proposion Design (projektowanie propozycji wartości) – ocena, jaką wartość dostarczamy obecnie klientom, a także projektowanie nowej propozycji wartości,
- Customer Experience Design – projektowanie doświadczenia klienta (zorientowane nie tylko na marketing, ale na cały łańcuch wartości),
- Design Thinking – projektowanie produktów i procesów zorientowane na klienta.
Z perspektywy wewnętrznej bardzo wartościowe będzie użycie sprawdzonych metod, np.
- Value Stream Mapping – wykorzystywane w metodologii Lean Management mapowanie, w jakim stopniu nasze procesy dodają wartość klientowi,
- Voice of Customer – narzędzie metodyki SixSigma pozwalające na uwzględnienie potrzeb klienta w procesach usprawnień.
Następnie ważna będzie ocena potencjalnego wolumenu produkcji (wielkość rynku) dla naszego portfolio, a także wybór strategii rynkowej (produkcja masowa, koncentracja, produkcja niszowa).
Taka wstępna analiza powinna pomóc w identyfikacji, na ile twoje produkty i procesy są konkurencyjne, a także wstępnie określić kierunek rozwoju. Kolejny krok, to wybór odpowiedniego archetypu dla fabryki.
Nowy archetyp fabryki
W opracowaniu „Industry 4.0 – how to navigate digitization of the manufacturing sector” z roku 2015 McKinsey proponuje ciekawą koncepcją 3 archetypów dla fabryk przyszłości (Smart-Automated Plant, Customer-Centric Plant, e-Plant in-the-box), które są zaklasyfikowane według realizowanego wolumenu produkcji oraz źródła wartości (koszty, personalizacja). Dyskusje z menedżerami firm produkcyjnych pokazują jednak, że takie podejście nie wyczerpuje tematu. Po pierwsze, nie można zgodzić się ze stwierdzeniem, że zorientowana na klienta powinna być tylko jedna grupa fabryk. Takie powinny być wszystkie. Dodatkowo w zakresie niskiego wolumenu produkcji i wysokiego stopnia personalizacji funkcjonuje (i w moim przekonaniu będzie funkcjonować) czwarta kategoria fabryk. Dlatego proponuję przyjęcie nowej klasyfikacji, w której fundamentem każdego archetypu będzie orientacja na klienta.
Cztery nowe archetypy fabryk przyszłości mogą wyglądać jak poniżej:
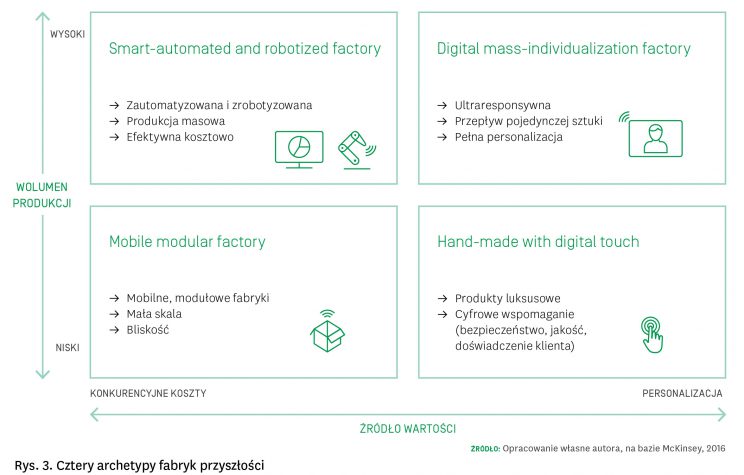
1.Smart-automated and robotized factory – „Inteligentna zautomatyzowana i zrobotyzowana fabryka”
Fabryka realizująca bardzo wysokie wolumeny produkcji, która dzięki pełnej automatyzacji i robotyzacji procesów jest w stanie wytwarzać produkty z niskim (niższym niż konkurencja) poziomem kosztów. Produkcja w niej jest zorganizowana w formie dedykowanych zautomatyzowanych linii produkcyjnych ze wspólnymi modułami konfekcjonowania. Taki model może przyjąć na przykład producent z branży spożywczej, który swój biznes opiera na współpracy z sieciami dyskontowymi
2. Digital mass-individualization factory – „Cyfrowa masowa indywidualizacja w fabryce”
Fabryka realizująca produkcję w zakresie średnich lub wysokich wolumenów produkcji wysoce indywidualizowanych produktów (np. samochody, ubrania, meble, elementy konstrukcyjne, bramy). Zakład pod względem procesowym i technologicznym jest przygotowany do realizacji bardzo krótkich serii, częstych przezbrojeń i wysokiej personalizacji produktu. Często jest on zorganizowany w formie uniwersalnych, modułowych gniazd produkcyjnych, gdzie produkt steruje przepływem sekwencji produkcji. To też jest produkcja zrobotyzowana i zautomatyzowana, tylko z innym rodzajem organizacji produkcji w formie np. gniazd.
3. Mobile-modular plant – „Mobilna modułowa fabryka”
Fabryka „mobilna”, czyli taka, która może być w sposób elastyczny budowana, uruchamiana, pakowana i przenoszona w zależności od trendów rynkowych, standardów branżowych lub dostępu do surowca. Przykładem minifabryki w takim archetypie może być system produkcji palet tekturowych, które zostały wprowadzone jako standard w grupie IKEA. Taki system ze względu na swoją mobilność może zostać bardzo szybko zbudowany, zamontowany i uruchomiony w dowolnym miejscu na hali produkcyjnej, lub też w jej bezpośredniej bliskości, na czas realizacji zlecenia. Kolejnym przykładem są minifabryki narzędzi i komponentów do realizacji dużych inwestycji budowlanych. Bardziej zaawansowany przykład – modułowa mleczarnia od Nestlé – został opisany dalej.
4. Hand-made with digital touch – „Produkcja ręczna z wykorzystaniem cyfryzacji”
To zupełnie nowy archetyp dotyczący niszowego segmentu rynku, który jednak odpowiada za produkcję produktów o najwyższej wartości jednostkowej (także segmentu produktów luksusowych). W takich fabrykach proces opiera się na ręcznej pracy najwyższej klasy specjalistów (często rzemieślników), którzy z wykorzystaniem nowoczesnych narzędzi do obróbki materiałów wytwarzają produkty na indywidualne zamówienie. W tego typu fabrykach nowoczesne technologie są wykorzystywane w sytuacjach, w których zwiększają bezpieczeństwo pracy, chronią zdrowie (np. zrobotyzowane malowanie), a także pomagają w podnoszeniu jakości doświadczenia klienta, czy też organizacji procesu produkcji (cyfrowy obieg informacji). Zgodnie z takim archetypem działają producenci luksusowych samochodów (np. Bentley, Ferrari), producenci w branży zbrojeniowej oraz aerospace.
Powyżej opisane zostały cechy różnicujące archetypy. Istnieje natomiast szereg zagadnień wspólnych (tzw. pryncypiów), które dotyczą każdego z nich. Należą do nich:
- rozwój kompetencji menedżerów, inżynierów i pracowników liniowych,
- dbanie o doskonałość operacyjną – kontynuacja programów ciągłego doskonalenia,
- rozwój infrastruktury cyfrowej i cyfrowy przepływ informacji – tzw. Paperless Factory,
- polityka i narzędzia w obszarze cyberbezpieczeństwa.
Kierunek zmian
W kierunku których archetypów migrują globalne i polskie firmy? Z pewnością liderzy branży automotive wybrali drogę „cyfrowej masowej indywidualizacji (ang. Digital mass-customization). W tej kategorii warto wyróżnić Toyotę, która z jednej strony inwestuje w nowoczesne technologie produkcyjne, z drugiej zaś rozwinęła wyjątkową kulturę organizacji pracy i organizacji procesów. Adidas z produkcji masowej niskokosztowej przesuwa się w kierunku masowej personalizacji i będzie produkował indywidualizowane buty w Niemczech. Zmienią się nie tylko fabryki, ale także punkty sprzedaży, które będę stanowiły ogniwo łańcucha produkcyjnego, wykorzystując technologie skanowania i drukowania 3D. Branża spożywcza (poza nielicznymi wyjątkami) pozostaje w obszarze produkcji masowej niskokosztowej, koncentrując się na redukcji kosztów wytworzenia a także efektywności energetycznej. Unikalny w obszarze łańcucha wartości wydaje się projekt w nurcie „mobilna modułowa fabryka” (ang. Modular factory) realizowany przez Nestlé. Bazuje on na pryncypiach Przemysłu 4.0, którymi są modułowość i decentralizacja. Nestlé zbudowało koncepcję modułowej mleczarni, która będzie mogła powstawać w czasie do 50% krótszym niż standardowa konstrukcja. Zaproponowane i ustandaryzowane zostały elementy konstrukcji budynku, paneli solarnych, gotowe elementy wyposażenia budynku w postaci sal, stołówki, itd. Ma to umożliwić standaryzację w obszarze projektowania i budowy fabryk jako kontynuację standaryzacji w obszarze technologii produkcyjnych i infrastruktury. Przykładem dla archetypu 4 – Hand-made with digital touch – może być wykorzystanie robotów malujących w produkcji luksusowych samochodów Lexus LFA.
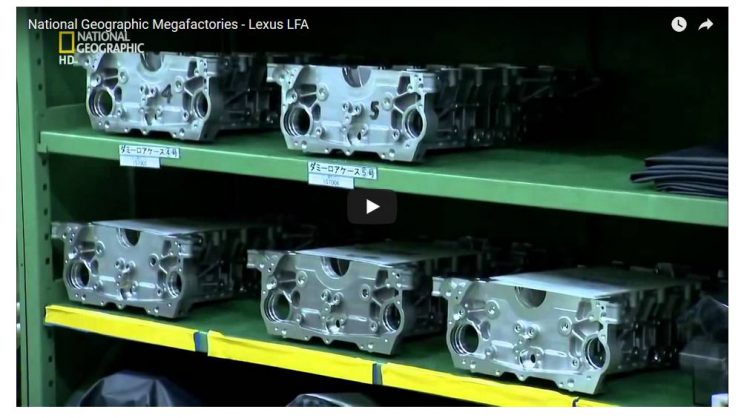
Dobre polskie przykłady
Szczęśliwie kilka polskich firm produkcyjnych także podejmuje pionierskie działania. Wśród nich można na pewno wyróżnić firmę Wiśniowski, która strategicznie zainwestowała we wszystkie ogniwa łańcucha wartości. Wybranym archetypem dla fabryk jest „cyfrowa masowa indywidualizacja” (ang. Digital mass-indivdualization). Cała sieć dystrybutorów posiada narzędzia, które umożliwiają personalizację produktu dla klienta końcowego. Dodatkowo, po złożeniu zamówienia, system informatyczny jest w stanie automatycznie wygenerować zamówienia na parametry technologiczne produkcji (w tym parametry pracy robotów spawalniczych). Dzięki integracji informatycznej pionowego łańcucha wartości, czas dostarczenia produktu finalnego skraca się znacząco, co przekłada się na wymierne korzyści biznesowe.
Przykładem dobrej, innowacyjnej praktyki w obszarze rozwoju łańcucha wartości jest firma Nowy Styl. W obszarze R&D firma powołała zespół badań i consultingu przestrzeni pracy. Zespół ten, wykorzystując metodykę Design Thinking, wspólnie z klientami wypracowuje nowe koncepcje organizacji przestrzeni biurowej. Następnie – we współpracy z technologami – przekłada te koncepcje na produkcję. Dodatkowo samo zaplecze produkcyjne z nowoczesnymi technologiami wspiera sprawną realizację zindywidualizowanych produktów.
Z pewnością każda branża produkcyjna może również zostać zakwalifikowana do konkretnych archetypów.
Przykład takiej kategoryzacji podaję na rys. 5.
Archetypy a poziom automatyzacji
Konsekwencją wyboru docelowego archetypu będzie oczywiście zmiana podejścia do projektowania i rozbudowy fabryk, gdzie nie wystarczy już klasyczne podejście architektoniczne. Bardzo ważne w tym procesie będzie uwzględnienie takich aspektów, jak organizacja procesów i przepływu produktu na halach produkcyjnych, organizacja logistyki wewnętrznej, wykorzystanie nowoczesnych technologii produkcyjnych, które będą wspierały efektywność i personalizację (np. automatyzacja produkcji i transportu, robotyzacja, cyfryzacja – w tym Internet Rzeczy, IIoT – czy wytwarzanie przyrostowe).
Każdy z archetypów ma zupełnie inne wymagania dotyczące automatyzacji. O ile w archetypie 1. – „inteligentna zautomatyzowana i zrobotyzowana fabryka” (ang. Smart-automated and robotized factory) – layout fabryki składać się będzie z klasycznych ciągów produkcyjnych, o tyle w fabrykach zorientowanych na masową indywidualizację (archetyp 2.: „cyfrowa masowa indywidualizacja w fabryce” (ang. Digital mass-individualization factory), będzie to raczej podejście do organizacji produkcji oparte o modułowe gniazda obróbcze, gdzie to produkt decyduje, z których gniazd skorzystać, żeby wyjechać z obszaru produkcji w jak najkrótszym czasie i w oczekiwanej jakości.
Z drugiej strony koszty technologii (np. robotów przemysłowych) w ostatnich 20 latach znacząco spadły. Dzięki temu inwestycje, które jeszcze kilka lat temu nie były rentowne, teraz już się opłacają. Co więcej, zaawansowane systemy wizyjne i pomiarowe (czujniki) pozwalają na automatyczne wykonywanie coraz bardziej zaawansowanych operacji. Dzięki temu zakres procesów podatnych na automatyzację stale się powiększa, powodując przy tym wzrost ROI (rys. 6).
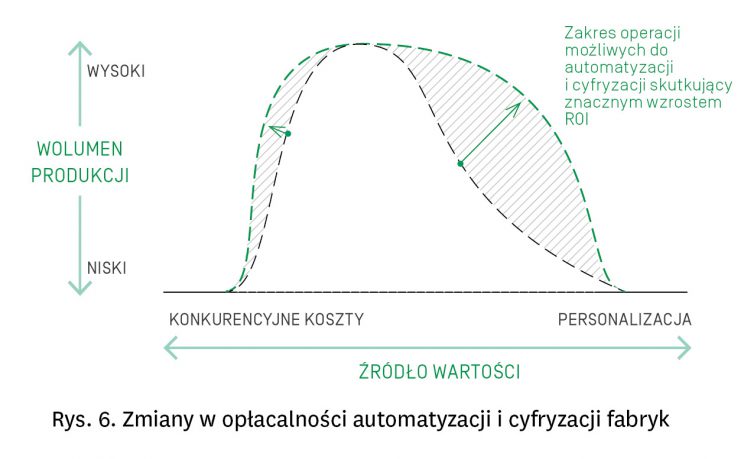
Co fabryka, to wyzwanie
Opisanych powyżej zagadnień nie można rozwiązać za pomocą jednej recepty. Każda fabryka powinna indywidualnie w gronie menedżerów i kluczowych inżynierów zastanowić się nad wizją swojej przyszłości. Najistotniejsze punkty, które warto przemyśleć – po analizie strategii rynkowej, w tym łańcucha wartości, oraz portfolio produktów – to:
- Jak rozbudowywać i modernizować istniejące fabryki?
- Jak projektować i budować nowe fabryki?
- Jak rozwijać procesy i technologie produkcyjne?
- Jak wykorzystać technologie cyfrowe do zwiększenia czasu pracy umysłowej kosztem czasu pracy fizycznej?
- Jak zmieniać nastawienie i rozwijać kompetencje kadry na każdym poziomie odpowiedzialności?
- Jak rozwijać inżynierów?
Na koniec zostawiam dwa kluczowe pytania:
Który archetyp fabryki najbardziej pasuje do twojej strategii rynkowej? Jak wdrożysz go w życie?
Jarosław Gracel
Członek zarządu operacyjnego, dyrektor ds. przemysłu 4.0 w firmie ASTOR.
Artykuł pierwotnie ukazał się w wydawanym przez ASTOR piśmie Biznes i Produkcja nr 17, dostępnym tylko dla prenumeratorów.