Treści
Nowe programy wsparcia przedsiębiorstw produkcyjnych
Nowe programy wsparcia przedsiębiorstw produkcyjnych
Wnioski na nowe formy dofinansowania będzie można składać w ciągu najbliższych miesięcy.
Najnowsza perspektywa unijnego wsparcia przewiduje całą gamę programów pomocowych. Prezentujemy te najważniejsze dla przedsiębiorstw produkcyjnych. Dodatkowo pokazujemy z jakich odliczeń już teraz mogą korzystać przedsiębiorstwa produkcyjne w Polsce.
Niezależnie od tego czy jesteś dyrektorem dużej fabryki, konsorcjum czy założycielem małego przedsiębiorstwa produkcyjnego (start-upu) możesz liczyć na unijne wsparcie swojej działalności w postaci bezzwrotnej dotacji, albo też ulgi podatkowej. Obiema formami wsparcia zainteresowanych jest coraz więcej polskich przedsiębiorstw, choć część z nich grzęźnie w gąszczu informacyjnym i nie wie co wybrać. Spróbujmy więc uporządkować dostępne opcje, zwłaszcza, że moment podjęcia decyzji jest już bliski. Być może nawet jeszcze w maju będzie można składać pierwsze wnioski na dotacje z nowej puli.
Zacznijmy od omówienia tego bezzwrotnego wsparcia
Procedura ubiegania się o dotacje, harmonogram składania wniosków zależne są od wielkości przedsiębiorstwa i lokalizacji. Niektóre programy mają charakter krajowy inne regionalny. Dlatego poszukiwania właściwej formy dofinansowania warto zacząć od analizy mapy wsparcia i ustalenia jakie programy dostępne są w twoim regionie kraju.
Instytucje, które udzielają takiego wsparcia, do których należy składać wnioski to Narodowe Centrum Badań i Rozwoju oraz Polska Agencja Rozwoju Przedsiębiorczości.
Oba podmioty oferują pomoc w postaci wyszukiwarek konkursów oraz punktów informacyjnych, dzięki którym przedsiębiorcy mogą lepiej dobrać dofinansowanie do swoich potrzeb.
Przedstawiamy wybrane programy, które mogą być interesujące dla przedsiębiorców z branży produkcyjnej. Zacznijmy od tych regionalnych.
1. Automatyzacja i robotyzacja w MŚP
To instrument wdrażany w ramach Programu Fundusze Europejskie dla Polski Wschodniej. Dotacja przeznaczona na zakup rozwiązań automatyzacyjnych i robotów przemysłowych, w tym całych rozwiązań z obszaru Przemysłu 4.0, także oprogramowania. Dotyczy obszaru Polski wschodniej. Jej przyznanie wymaga przeprowadzenia audytu technologicznego i opracowania mapy drogowej transformacji
Maksymalna wartość dofinansowania projektu to 3 mln PLN. Nabór wniosków rozpocznie się 1 sierpnia 2024 roku i potrwa do 26 września.
2. Wdrażanie technologii cyfrowych w MŚP – Bon na cyfryzację (Podlasie)
To pokrewna inicjatywa skierowana także do firm działających w Polsce wschodniej, a konkretnie na Podlasiu.
Dofinansowanie można przeznaczyć na zakup oprogramowania i usług, a także w ograniczonym zakresie środków trwałych w obszarze, produkcji, procesów i produktów. Celem inwestycji może być też podniesienie poziomu cyberbezpieczeństwa. Program adresowany jest do mikro, małych i średnich przedsiębiorstw.
Maksymalna wysokość dofinansowania to 150 tys. PLN. Nabór wniosków została zaplanowany na II kwartał 2024 roku, co oznacza, że może ruszyć jeszcze przed wakacjami.
3. Wdrożenie rozwiązań w zakresie Przemysłu 4.0 (Łódzkie)
To dofinansowanie dla małych i średnich przedsiębiorstw z województwa łódzkiego. Otrzymane środki mogą zostać przeznaczone w szczególności na zakup robotów przemysłowych, zaawansowanych technologii cyfrowych i specjalistycznego oprogramowania dla rozwiązań z obszaru Przemysłu 4.0. Dofinansowanie ma pomóc we wdrażaniu technologii cyfrowych z co najmniej jednego z poniższych obszarów:
- BigData, analiza danych
- roboty przemysłowe
- przemysłowy internet rzeczy (IoT)
- sztuczna inteligencja (AI)
- druk 3D
- wirtualna rzeczywistość
- chmura obliczeniowa
- cyberbezpieczeństwo
- integracja IT/OT
- blockchain
- łączność w technologii 5G
- technologie kwantowe (Quantum Computing)
- mikroelektronika
Maksymalna kwota dofinansowania to 1mln PLN. Nabór wniosków prowadzony będzie pomiędzy 16 a 30 września 2024 r.
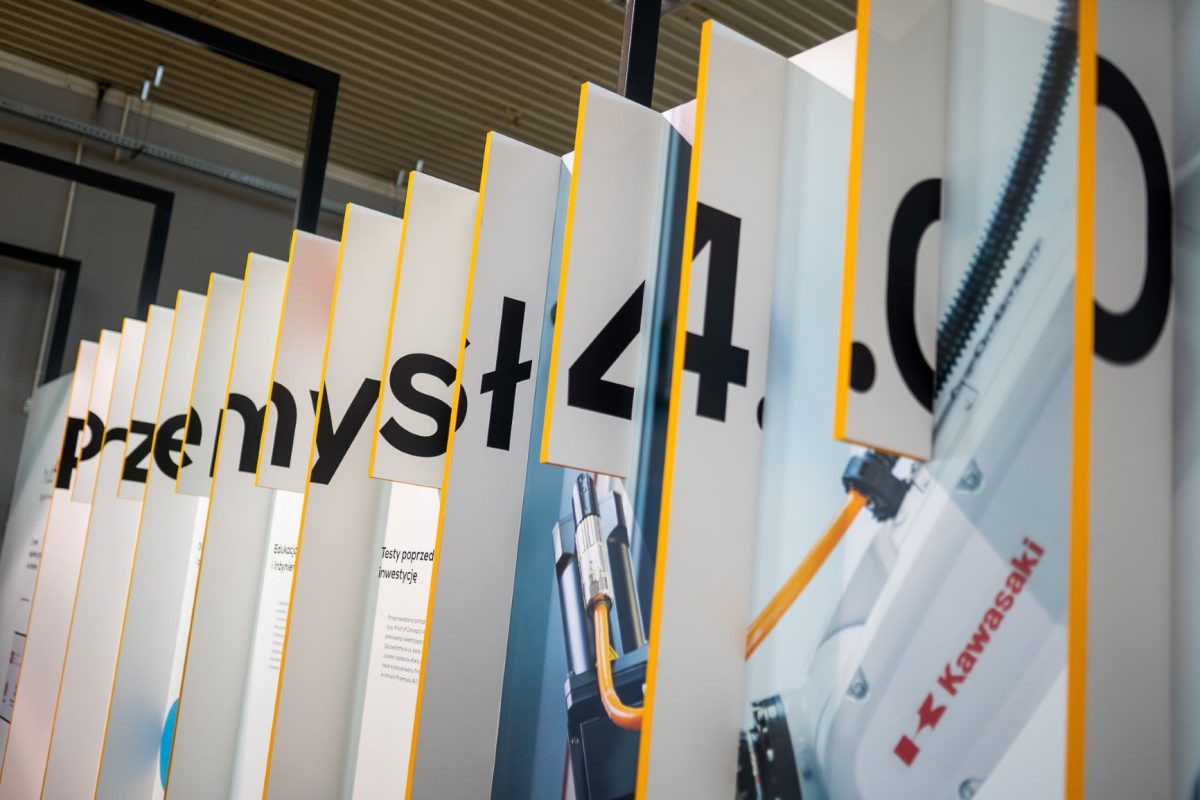
Przejdźmy teraz do programów ogólnokrajowych:
4. Ścieżka SMART (FENG)
To jedno z ważniejszych, jeśli nie najważniejsze narzędzie wsparcia Przemysłu 4.0 w Polsce. Celem tego instrumentu jest wspieranie małych i średnich przedsiębiorstw w działalności innowacyjnej, ale też konsorcjów i dużych przedsiębiorstw oraz konsorcjów naukowo-przemysłowych. Dofinansowanie dotyczy podmiotów z całej Polski.
Skrót FENG oznacza Fundusze Europejskie dla Nowoczesnej Gospodarki. To program operacyjny UE podzielony na działania.
Przedsiębiorstwa z sektora MŚP, zainteresowane udziałem w naborze, muszą uwzględnić w swoich wnioskach jeden z dwóch modułów obligatoryjnych: moduł B+R lub moduł wdrożenie innowacji. Duże muszą zawsze mieć w projekcie moduł prac B+R. Ponadto do wyboru są moduły fakultatywne:
- infrastruktura B+R (inwestycje w infrastrukturę badawczą, np. utworzenie lub rozbudowa centrów badawczych);
- cyfryzacja;
- zazielenienie (transformacja w kierunku gospodarki obiegu zamkniętego);
- internacjonalizacja (promocja zagraniczna produktów lub usług przedsiębiorstwa);
- kompetencje (doskonalenie kompetencji pracowników i osób zarządzających).
Możliwe jest złożenie wniosku o dofinansowanie projektu obejmującego wszystkie siedem modułów. Poszczególne moduły mogą być realizowane jeden po drugim jako poszczególne działania. Przedsiębiorca może również dobierać do projektu moduły, w których będzie realizował działania niekoniecznie powiązane z pracami B+R czy wdrożeniem innowacji.
Chcesz wiedzieć więcej, przejdź do artykułu: FENG – jak pozyskać finansowanie dla Przemysłu 4.0.
Czytaj!
Nabory dla przedsiębiorstw (MŚP i dużych) ruszą 27 czerwca 2024 r. i potrwają do 24 października. Nabory dla konsorcjów rozpoczną się 10 stycznia 2025 r. i potrwają do 28 marca 2025 r.
5. DIG.IT Transformacja cyfrowa polskich MŚP (ARP)
To instrument Agencji Rozwoju Przemysłu przeznaczony dla mikro, małych i średnich przedsiębiorstw działających na terenie całego kraju. Wsparcie ułatwia zakup technologii cyfrowych (oprogramowania), środków trwałych (sprzętu IT) oraz przeprowadzenie szkolenia pracowników.
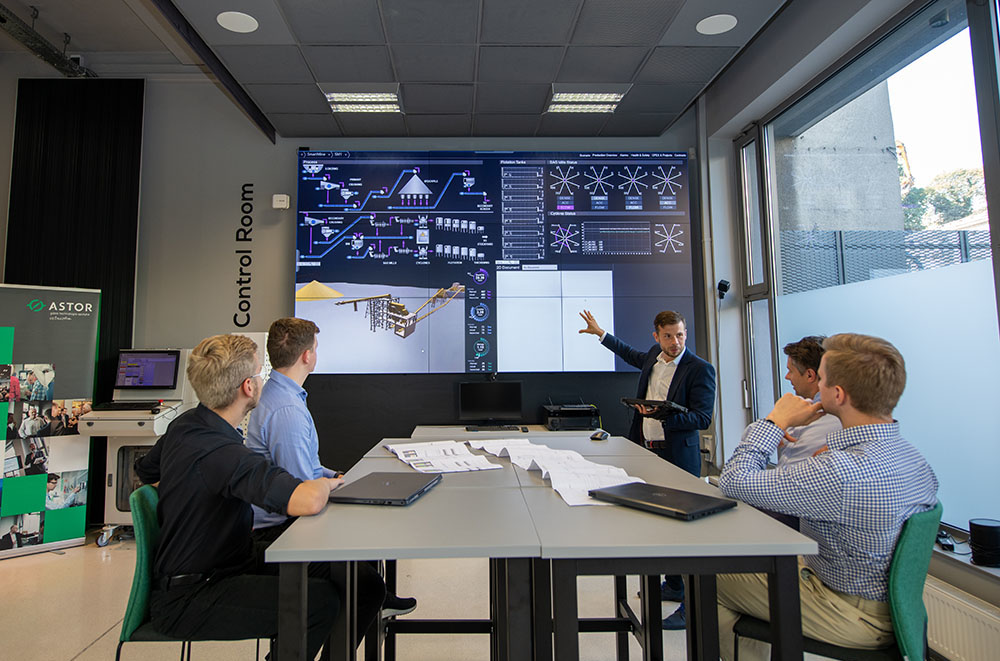
W wydatkach, na które zostaje przyznane dofinansowanie muszą znaleźć się:
- Zakup oprogramowaniu lub zlecenie prac programistycznych w celu jego opracowania
- Usługi chmurowe typu Saas, Paas, Iaas, CsaaS
Można też (choć nie trzeba) z przyznanych środków opłacić koszty wdrożenia oprogramowania, szkolenia z obsługi, koszty niezbędnego sprzętu. Dofinansowanie może maksymalnie sięgnąć 200 tys. Euro (do 50% wartości inwestycji).
Preferowane obszary, których dotyczyć mają inwestycje to:
- Przemysł/produkcja
- Mikro i małe przedsiębiorstwa
- Projekty kompleksowe
- Ekoinnowacje
Nabór wniosków została zaplanowany na II kwartał 2024 roku, co oznacza, że może ruszyć jeszcze przed wakacjami.
Ulgi podatkowe – co trzeba wiedzieć?
Ulgi nie wymagają dodatkowych starań, po prostu można rozliczać je w zeznaniach podatkowych. W przytłaczającej większości nie mają końcowej daty ważności. Wyjątek stanowi ulga na robotyzację, którą można uwzględniać w zeznaniach do 2026 roku. W raporcie, który powstał na 20 lecie wejścia Polski do UE, “Zachęty inwestycyjne i ulgi podatkowe dla przedsiębiorców po wejściu Polski do UE”, przygotowanym przez CRIDO, autorzy zauważają, że ulgi nie są znane polskim przedsiębiorcom.
Tak opisują te ulgi, które są najistotniejsze z punktu widzenia firm produkcyjnych:
Ulga B+R
Obowiązuje od 2016 roku. Polega na możliwości dodatkowego odliczenia od podstawy opodatkowania do 200% wydatków związanych z prowadzeniem szeroko rozumianej działalności badawczo-rozwojowej.
Ulga na innowacyjnych pracowników
Stosowana w przypadku, w którym podatnik osiągnął stratę lub nie wykorzystał w pełni korzyści podatkowej z ulgi B+R w danym roku podatkowym. Polega na możliwości pomniejszenia w następnym roku podatkowym zaliczki na podatek dochodowy (PIT) płatnej z tytułu umów o pracę pracowników czy też z umów zlecenia lub umów o dzieło współpracowników zaangażowanych przynajmniej w 50% w projekty B+R.
Ulga na prototyp
Polega na możliwości dodatkowego odliczenia od podstawy opodatkowania do 30% kosztów uzyskania przychodów dotyczących produkcji próbnej i wprowadzenia na rynek nowego produktu powstałego w wyniku działalności badawczo-rozwojowej.
Ulga na ekspansję
Polega na dodatkowym odliczeniu od podstawy opodatkowania wydatków na marketing, promocję i reklamę, poniesionych w celu zwiększenia przychodów ze sprzedaży wyprodukowanych przez podatnika produktów (maksymalnie do 1 miliona PLN w danym roku podatkowym).
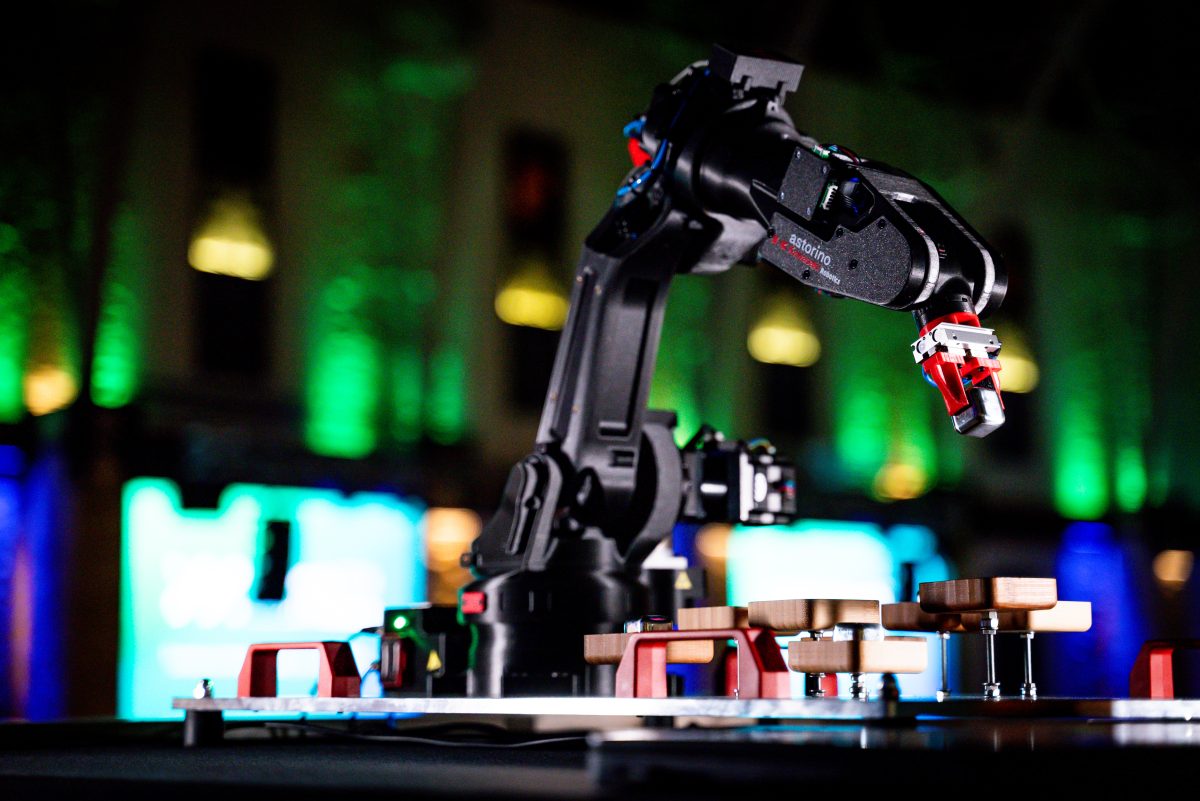
Ulga na robotyzację
Polega na możliwości dodatkowego odliczenia od podstawy opodatkowania – do 50% kosztów uzyskania przychodu – wydatków na robotyzację (zakup nowych robotów i urządzeń z nimi powiązanych). Ulga ma charakter czasowy i obowiązuje w latach 2022–2026.
IP BOX
Polega na możliwości zastosowania podatku dochodowego w wysokości 5% w odniesieniu do dochodów uzyskiwanych przez podatnika z tzw. kwalifikowanych IP opracowanych lub rozwiniętych w ramach działalności B+R. Do kwalifikowanych IP zaliczyć można m.in.: patent, prawo ochronne na wzór użytkowy lub przemysłowy czy autorskie prawo do programu komputerowego.
Ulga na sponsoring
Polega na możliwości dodatkowego odliczenia od podstawy opodatkowania do 50% kosztów uzyskania przychodów poniesionych na działalność: sportową, kulturalną oraz wspierającą szkolnictwo wyższe i naukę.
Dotacje czy ulgi podatkowe
Jak przekonują autorzy opracowania CRIDO, pozyskanie dotacji w żadnym wypadku nie oznacza braku możliwości skorzystania z ulg podatkowych (w przypadku niektórych ulg wpłynie to tylko na poziom dostępnego odliczenia). W przypadku ulg podatkowych, których bazą jest odliczenie kwalifikowanych kosztów podatkowych od podstawy opodatkowania (np. ulga B+R), pozyskanie dotacji spowoduje, że ulgami możliwe będzie objęcie tylko niedotowanych kosztów kwalifikowanych (czyli niemożliwym jest uzyskanie dwukrotnej korzyści w postaci dofinansowania i odliczenia od dochodu tych samych kosztów).
Dla przykładu w ramach ulgi B+R może być rozliczany wkład własny poniesiony przez beneficjenta dotacji na działalność B+R (na przykład w ramach dotacji pozyskanej w programie Ścieżka SMART). Niemniej, zasada ta nie ma zastosowania do IP Box, w przypadku którego pozyskanie dotacji nie wpływa na zakres stosowania ulgi (czyli można komercjalizować IP wytworzone w ramach projektu B+R, na który otrzymano dofinansowanie). Zatem dotacje nie wykluczają ulg podatkowych, ale w każdym wypadku wymagana jest weryfikacja kosztów kwalifikowanych, które zostały uwzględnione w ramach dotacji, oraz tych, które kwalifikują się do objęcia ulgami podatkowymi.