Treści
Jak kontrolować CAPEX by minimalizować OPEX?
Jak kontrolować CAPEX by minimalizować OPEX?
Optymalizacja i automatyzacja produkcji czy transportu wewnątrzzakładowego zwiększa wydajność procesów. Umiejętnie alokowane nakłady inwestycyjne prowadzą jednak nie tylko do wzrostu efektywności, ale też do redukcji kosztów operacyjnych w całym przedsiębiorstwie.
Budżet przedsiębiorstwa, czy poszczególnych linii zadaniowych tworzony jest przez wpływy finansowe oraz wydatki CAPEX i OPEX. Umiejętne inwestowanie w technologie może prowadzić nie tylko do zwiększenia wydajności, ale też redukcji kosztów operacyjnych.
CAPEX z definicji (ang. capital expenditures, pol. wydatki inwestycyjne, nakłady kapitałowe) – to fundusze wykorzystywane do nabywania, ulepszania i utrzymywania aktywów fizycznych, takich jak nieruchomości, budynki, zakłady przemysłowe, technologie lub sprzęt.
Wydatki tego rodzaju tworzą przyszłe korzyści dla przedsiębiorstwa, poprzez zwiększenie użyteczności posiadanych aktywów lub zakup nowych. CAPEX jest często wykorzystywany do podejmowania przez firmę nowych projektów lub inwestycji.
Do wydatków typu CAPEX zaliczane są sumy wydane na:
- zakup aktywów trwałych, także niematerialnych,
- naprawy posiadanych aktywów w celu zwiększenia ich użyteczności,
- modernizacje posiadanych aktywów,
- przygotowanie aktywów do wykorzystania w działalności przedsiębiorstwa,
- adaptowanie nieruchomości lub aktywów do innego użytku,
- rozpoczęcie nowej działalności lub przejecie innego przedsiębiorstwa.
Jeśli chodzi o rachunkowość, koszt jest uważany za wydatek inwestycyjny (CAPEX), gdy składnik aktywów jest:
- nowym nabytkiem,
- inwestycją, której żywotność przekracza jeden rok,
- inwestycją, która poprawia okres użytkowania istniejącego środka trwałego.
Wydatki na przedmioty, takie jak sprzęt, który ma okres użytkowania krótszy niż jeden rok, muszą zostać ujęte w kosztach utrzymania (OPEX).
OPEX jest pojęciem powiązanym z CAPEX. OPEX (ang. operational expenditures, pol. koszty utrzymania, wydatki operacyjne) to bieżące koszty utrzymania firmy, systemu, czy produktu, rozpatrywane w perspektywie roku podatkowego.
Koszty utrzymania (OPEX) to nakłady ponoszone w związku z procesami użytkowania aktywów, a nie samymi aktywami. Obejmują̨ one także koszty ogólne. Koszty utrzymania (OPEX) mogą̨ obejmować:
- koszty administracji,
- koszty sprzedaży,
- koszty marketingu,
- opłaty księgowe i prawne,
- opłaty bankowe,
- nieskapitalizowane wydatki na badania i rozwój,
- koszty materiałów biurowych,
- koszty wynajmu i mediów,
- koszty bieżących napraw i konserwacji,
- koszty wynagrodzeń.
W przeciwieństwie do długoterminowych nakładów inwestycyjnych (CAPEX), koszty operacyjne (OPEX) są krótkoterminowe i mogą̨ być w pełni odliczone od podatków spółki w tym samym roku, w którym występują wydatki.
Co mówią CAPEX i OPEX?
Nakłady inwestycyjne (CAPEX) to każdy rodzaj wydatków, które spółka kapitalizuje lub wykazuje w swoim bilansie jako inwestycję, a nie na rachunku zysków i strat jako wydatek. Budżet CAPEX mówi zatem, ile firma inwestuje w istniejące i nowe środki trwałe w celu utrzymania się̨ lub rozwoju.
Natomiast porównanie całkowitego kosztu utrzymania (OPEX) ze sprzedażą̨ netto jest miarą rentowności przedsiębiorstwa oraz efektywności zarzadzania – jest to tzw. wskaźnik operacyjności. Mniejsza wartość wskaźnika operacyjności oznacza większą̨ efektywność wytwarzania przychodów w porównaniu z całkowitymi wydatkami firmy.
Nakłady inwestycyjne (CAPEX) nie są̨ przy tym wliczane do kosztów utrzymania, odliczana jest jedynie rata amortyzacyjna.
Co ważne, CAPEX i OPEX są ściśle od siebie zależne. CAPEX ma potencjał rozwojowy pozwala tworzyć nowe rozwiązania systemowe, które zwiększają potencjał konkurencyjny organizacji, ale najczęściej wykorzystanie nowych technologii oznacza też optymalizację procesów. Po stronie kosztów: redukcję strat efektywności, redukcję zbędnego obciążenia maszyn i załogi, redukcję przestojów. Po stronie zwiększenia przychodów: zwiększenie wydajności operacyjnej (przepustowości), szybszy Time-to-Market oraz Time-to-Volume czy zwiększenie wiarygodności u klientów obecnych oraz przyszłych. To wszystko przekłada się na możliwość poczynienia znacznych oszczędności w wymiarze operacyjnym (OPEX). Dlatego umiejętne alokowanie środków inwestycyjnych może być nie tylko sposobem na rozwój, ale też na optymalizację kosztów operacyjnych.
Artykuł powstał na bazie opracowania “Finanse Przemysłu 4.0”. Raport ten jest źródłem dodatkowych informacji na temat finansów firmy w realiach czwartej rewolucji przemysłowej. Zachęcamy do lektury: https://www.astor.com.pl/finanse40.html
Jak w praktyce wygląda dynamika CAPEX i OPEX w branży intralogistycznej? Prezentujemy dwa studia przypadku:
Przykład Eurotherm
Firma Eurotherm należąca do grupy Watlow jest liderem produkcji elektronicznych przyrządów kontrolno-pomiarowych, takich jak sterowniki, rejestratory czy kontrolery mocy. Zarząd w polskim oddziale zdecydował się zainwestować w automatyzację transportu wewnętrznego produktu gotowego za pomocą robota mobilnego MiR 250 firmy Mobile Insustrial Robots. Tego rodzaju inwestycja to właśnie CAPEX.
Automatyzacja pozwoliła zrezygnować ze żmudnego i rutynowego procesu. Gdy prace związane z transportem wewnątrz zakładowym były wykonywane ręcznie przez monotonie negatywnie wpływały na morale zespołu i generowały koszty (OPEX).
Użycie autonomicznego robota mobilnego do transportowania produktu gotowego do obszaru działu wysyłek, zwiększyło efektywność samego procesu, dzięki powtarzalności i szybkości działania. Uwolniło jednocześnie czas pracowników pozwalając im wykonywać zadania o dużej wartości dla przedsiębiorstwa, jak kompletacja, pakowanie i wysyłanie kompletnych zamówień.
MiR250 pracuje w systemie dwuzmianowym wykonując różne misje, wybierane z palety 12 zaprogramowanych zadań, w zależności od aktualnych potrzeb produkcji. Misje są uruchamiane bezpośrednio przez pracowników linii produkcyjnych. Średnio w ciągu dnia, robot pokonuje od 8 do 10 kilometrów, dostarczając do działu wysyłek średnio 900 gotowych produktów.
Robot wyposażony jest w moduł umożliwiający zdalne połączenie z oprogramowaniem, które zbiera dane o wykonanych misjach. Rozwiązanie to służy ponadto do prowadzenia diagnostyki zdalnej robota i pozwala na szybkie reagowanie. Usługa serwisowa robotów mobilnych, pozwala zminimalizować koszty (OPEX) związane z naprawami i utrzymaniem robota.
Szczegóły w artykule: “Jak zautomatyzować transport wewnętrzny produktu gotowego – na przykładzie Eurotherm”.
Przykład Flokk
Firma FLOKK produkuje meble biurowe i sprzedaje je w 80 krajach, na czterech kontynentach. Jej nazwa po norwesku oznacza stado, co dobrze odzwierciedla profil organizacji. Firma zarządza dziewięcioma markami, z których najstarsza (Giroflex) liczy ponad 150 lat. W „stadzie” jest też polska marka Profim. Zarząd polskiego oddziału FLOKK, gdzie produkowane są meble tej marki postanowił zainwestować w nowoczesny system do kompletacji i transportu wewnątrzzakładowego (CAPEX).
Sterowany cyfrowo system transportu wewnątrzzakładowego przyspieszający kompletację komponentów, montaż i pakowanie krzeseł biurowych, działa w zakładzie produkcyjnym w Turku w pobliżu Konina. Integruje trzy główne etapy:
- kompletowanie zestawów montażowych,
- transfer wraz z funkcjami buforowania do gniazd montażowych,
- transfer złożonych wyrobów gotowych do obszaru pakowania.
Inwestycja w nowoczesną linię kompletacji montażu krzeseł korzystnie wpłynęła na pozycję rynkową firmy, ponieważ zwiększyła możliwość szybkiego reagowania na potrzeby rynku i osiąganie wysokich wydajności. System międzyoperacyjny poprawiający logistykę produkcji, przyspieszył oraz poprawił jakość montażu. Operator koncentruje się na operacjach dodających wartość w procesie wytwarzania (Value Add Operation). Organizacja pracy obszaru, kompletacja, dostawy wspiera automatyzacja.
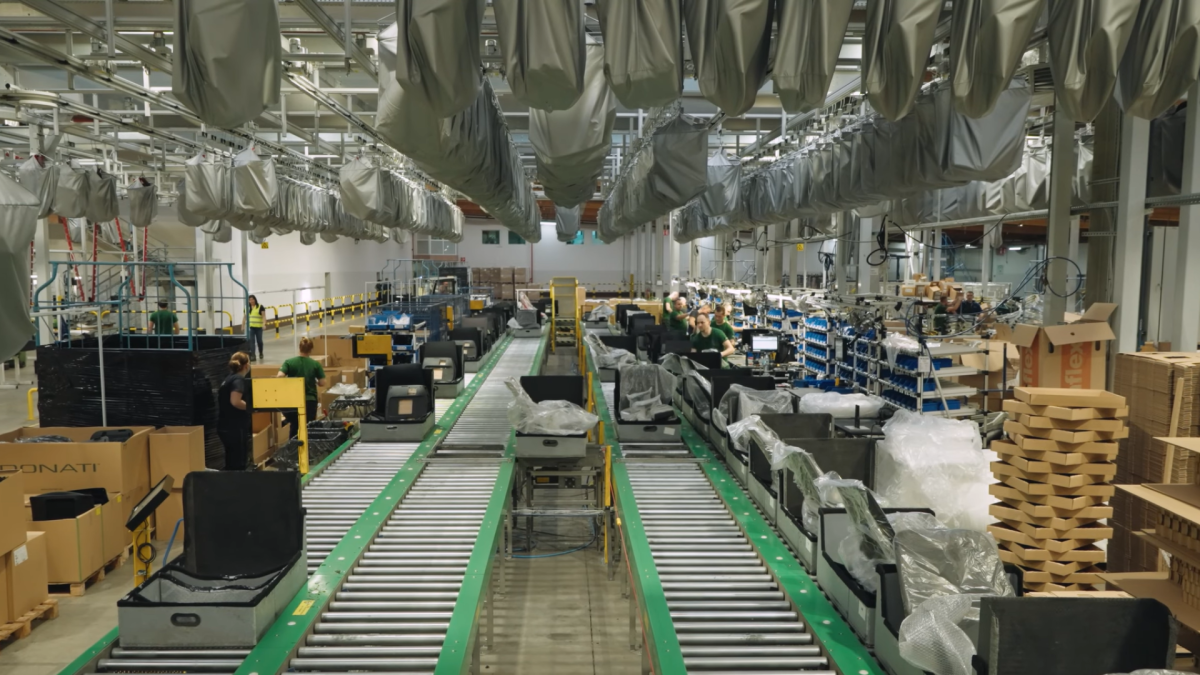
System pozwala osiągać założone cele wydajnościowe przy montażu kompletnego produktu gotowego. Daje też możliwość ciągłego monitorowania procesu. Jest zintegrowany z zakładowym systemem MES, dzięki czemu można śledzić wiele parametrów. Obok tych kluczowych, efektywnościowych również parametry diagnostyczne, które w kolejnym kroku są analizowane pod kątem utrzymania ciągłości pracy linii. Wszystkie powyższe mają swoje odbicie w planowanych nakładach wydatków operacyjnych OPEX. W trakcie przygotowania projektu ważne były zarówno parametry efektywnościowe procesu produkcyjnego jak i te finansowe. Ocena ryzyka oraz kryterium optymalnego TCO (Total Cost of Ownership) w stosunku do uzyskanych korzyści miały kluczowe znaczenie w procesie podejmowania decyzji o uruchomieniu inwestycji.
TCO = CAPEX + OPEX (w zakresie ocenianej inwestycji)
Szczegóły w artykule: “Logistyka produkcji i efektywny transport wewnątrzzakładowy – na przykładzie firmy FLOKK”.