Kawasaki robot palletises building materials and increases production efficiency at Siniat
Goals:
- Improved production efficiency
- Reduced workload and staff turnover
- Modernised production plant
Challenges:
- Efficient palletising of bags not only of different sizes and weights but also of bags with different fillings
Products/solution/ services:
- Kawasaki palletizing robot
Benefits:
- Productivity increase of approx. 25-30% with prospects for further improvement
- Savings in time and money
Company description
Siniat is a leading manufacturer of solutions for interior and exterior drywall systems and is part of the Etex Group – a global manufacturer of construction materials. In Poland, there are 3 plants producing plasterboards, metal profiles and gypsum mixtures. Siniat, as the main supplier and technical advisor for thousands of construction projects throughout the country, offers the best solutions and advises partners on how to make their homes, schools, hospitals and workplaces drier, quieter, warmer and safer.
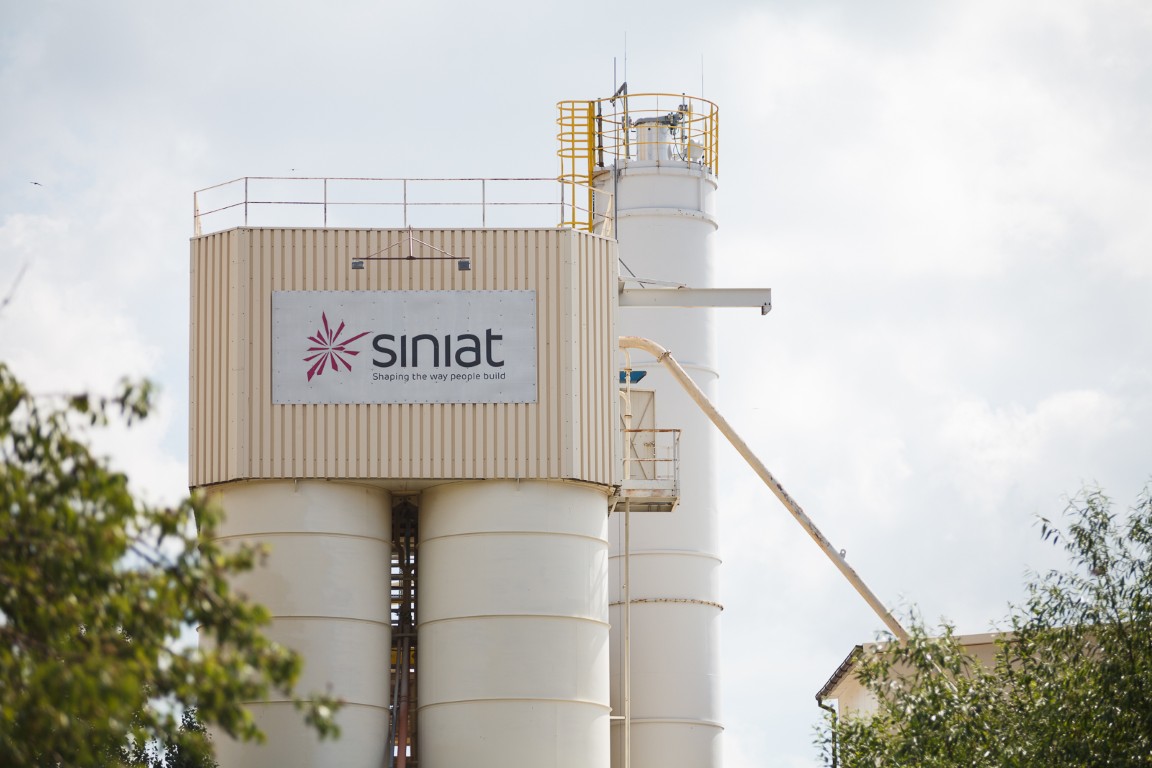
Needs
At the Siniat plant in Konin, which manufactures gypsum mixes, it was decided to automate the palletising station.
One of the obvious reasons for companies to introduce automated workstations into production facilities is to increase production efficiency. This was also the case here. Before deciding to invest, Siniat examined the extent to which productivity could be increased. The projected changes were significant, which determined the implementation of the investment. In addition, attention was drawn to additional benefits, i.e. time and financial savings.
“The clear expectations of Siniat’s technical department staff, their curiosity and understanding of the needs combined with the flexibility of the iPS Control’s engineers as well as a solid hardware platform, resulted in a system optimised already at the implementation stage. This is a solid and interesting project, which iPS Control carried out together with the Customer thanks to teamwork” Krzysztof Biliński, Technical Director at iPS Control
Another need of the company was to reduce employee rotation and, what is extremely important, to maintain safe working conditions related to the new solution, while complying with all standards arising from the Labour Code. Before the creation of the automated palletising station, Siniat’s employees operated a mechanical scissor lift and thus placed bags on pallets. The manual lifting equipment was intended to relieve the workers of the workload, giving them only the possibility to control the equipment. However, operating the lift without using much force required a high degree of equipment skill and experience which, in the case of new employees, posed a challenge in terms of applying the correct training.
After analysing the situation, it became clear that an automated palletising station could be the answer to all the company’s needs.
Implementation
When deciding to invest in automation, Siniat considered both industrial robots and palletisers. However, due to space availability at the plant, only robots could be considered. The advantage of the robot was its size and the ease with which it could be quickly implemented in the plant, without having to reorganise the production lines. Robots from various well-known manufacturers were considered. The final decision to choose Kawasaki ZD130SDE43 was made by the Board of Directors together with the Engineering Department, taking into account a solid brand of the product and very good opinions about the robots, which are supported by references from many companies, known all over the world.
The rapid implementation of the solution was handled by iPS Control. The challenge was to plan how to stack bags – not only of different sizes and weights but also bags with different fillings – on pallets. Siniat’s Manager of the Maintenance Department, Mariusz Jagodziński, and Automation Manager, Paweł Szymański, decided to take advantage of the ASTOR Academy’s training offer concerning the use of Kawasaki robots, and they say:
“The training provided knowledge that was useful during the implementation, which ultimately greatly accelerated the start-up and operation of the robot, and the training itself showed practical benefits, including in the area of occupational safety”.
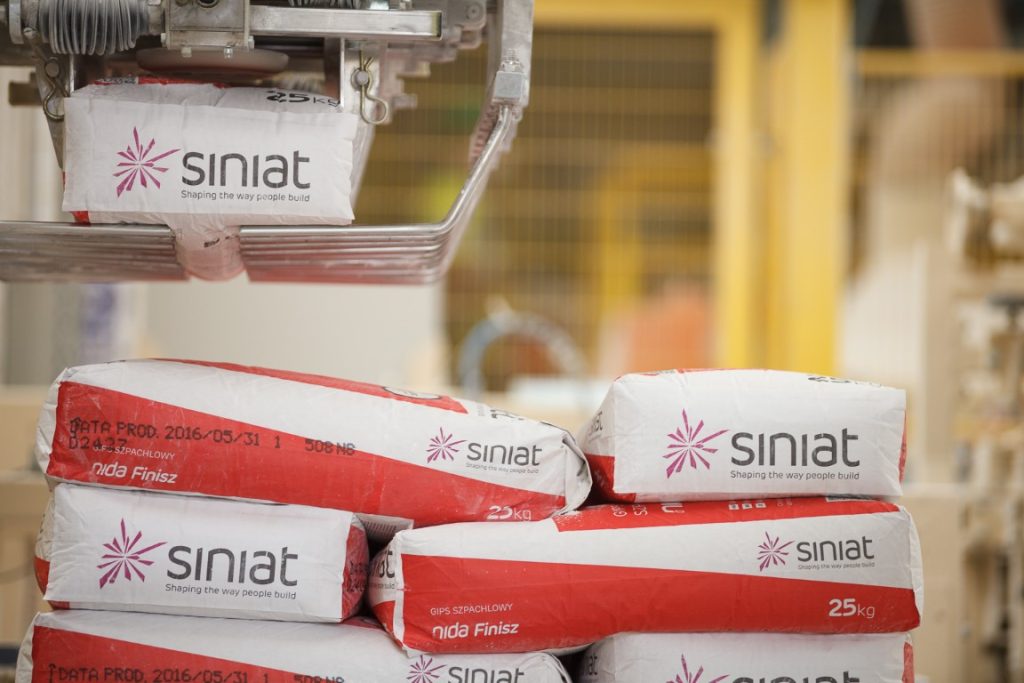
The way the bags are arranged depends on the size of the bags with building materials, weighing between 12.5 and 25 kg. However, the weight and dimensions of the bags are not a limitation. There is still opportunity for expansion, as the robot is currently operating at two-thirds of its capacity. Therefore, in the near future, the company plans to additionally extend palletising to 5 kg bags.
“The robotic bag palletising line, implemented by iPS Control for Siniat, was a multi-level project, which on the one hand represented a typical standard end-of-line solution, consisting of a palletising robot, an automated palletiser, a dynamic checkweigher with a
non-compliant bag rejection system and a number of conveyor systems, but on the other hand, there were a number of engineering challenges, related to limited space for the location of all palletising line elements, the multiplicity of products to be palletised (different shape, weight, physical properties of the raw material), the variety of palletising schemes, difficult external conditions (dustiness) or the high quality standards set by Siniat. Therefore, we decided on a flexible solution based on the Kawasaki palletizing robot, GE hardware platform with the RX3i main processor and Wonderware InTouch software for visualisation of the processes taking place in the palletising line” – says Krzysztof Biliński, Technical Director at iPS Control.“Significant productivity improvements due to the robotisation of the palletising process have allowed us to increase production efficiency, which is evident in real time and financial savings” Mariusz Jagodzinski, Manager of the Maintenance Department at Siniat.
The two-section robot gripper designed and manufactured by iPS Control provided adequate precision of movement, while minimising changeover (product variety), maintenance and service time. Thanks to the use of the proprietary DOTup solution, that is a largescale production data presentation system, all information about current production, order, performance, downtime, etc. is visible from anywhere on the palletising line. DOTup is a complementary part of the whole project, which is standard on the one hand, but poses an interesting engineering challenge on the other.
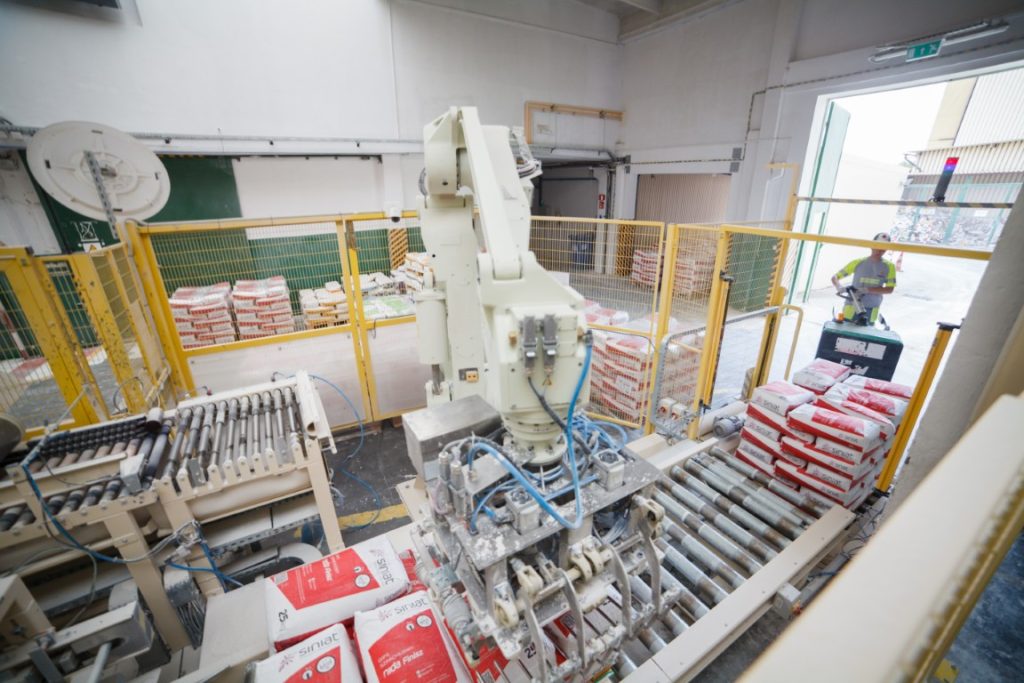
Benefits
The implementation made has mainly contributed to a 25-30% increase in productivity. It is worth remembering that the production process has not changed. What has been changed is one station responsible for palletising the finished products. This shows how much benefit robotisation can bring, allowing better use of existing production capacity. Currently, two persons are involved in operating the robot, but its operation does not require employees to be constantly present. It is just one of their many duties. Palletising operations are performed much faster by the robot than by workers. At the moment, their work is more about logistics and operating the station. This allows for additional development, which can further benefit Siniat. All these aspects contribute to the employees’ perception of their workplace.