Historie sukcesu
Jak dzięki mapie drogowej zaplanować transformację
Jak dzięki mapie drogowej zaplanować transformację
Projektowanie cyfrowej zmiany może być okazją do dokonania głębokiej restrukturyzacji w wymiarze kompetencyjnym i organizacyjnym – na przykładzie firmy Supron 3.
Od 1992 roku założona w Radomiu firma Supron 3 produkuje najwyższej jakości sprzęt przeciwpożarowy, hydranty wewnętrzne, szafy ochronne, węże pożarnicze oraz ekwipunek osobisty strażaków. Jak wiele polskich przedsiębiorstw produkcyjnych stanęła przed perspektywą dokonania transformacji cyfrowej zgodnej z założeniami czwartej rewolucji przemysłowej. Zarząd zainteresował się pozyskaniem dofinansowania z funduszy Unii Europejskiej. Jednym z wymogów było przygotowanie tzw. mapy drogowej transformacji. Wprawdzie dotacja miała wspomóc implementację jednego konkretnego rozwiązania technicznego, ale przygotowanie mapy stało się okazją do podjęcia głębokiej refleksji na temat całej firmy, zarówno w wymiarze organizacyjnym, technologicznym jak i ludzkim.
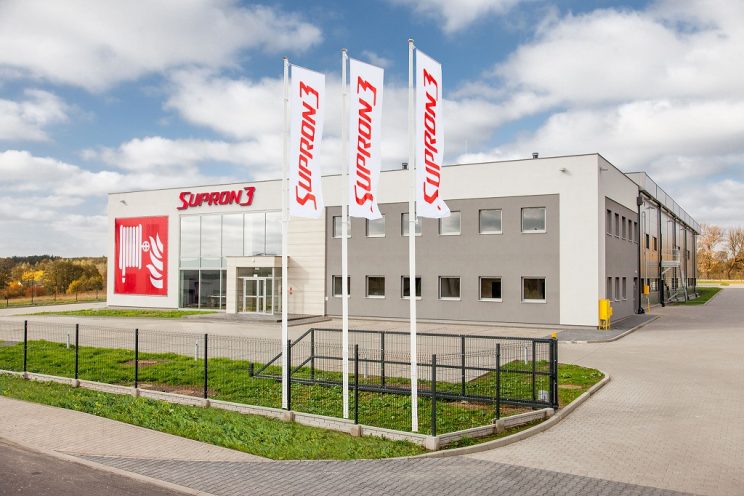
Jak dobrać partnerów
Kiedy przedstawiciele kadry kierowniczej dowiedzieli się, że jednym z wymogów uzyskania dofinansowania jest przygotowanie mapy drogowej, początkowo nie mieli pełnej jasności co do tego, czym ona właściwie jest i jak podejść do jej opracowania. Wysłali zapytania do kilku firm, w poszukiwaniu wsparcia. Zgłosiły się dwie. Ostatecznie po odbyciu szeregu rozmów zarząd zdecydował się na współpracę z firmą ASTOR. O wyborze przesądził między innymi fakt, że Supron 3 i ASTOR współpracowały już wcześniej przy implementacji zrobotyzowanej celi spawalniczej.
Po pierwszych spotkaniach stało się jasne, że mapa drogowa to dokument wskazujący kierunek transformacji do przemysłu 4.0 i szczegółowo opisujący poszczególne etapy tego procesu. Jego przygotowanie też podzielone jest na jasno określone fazy.
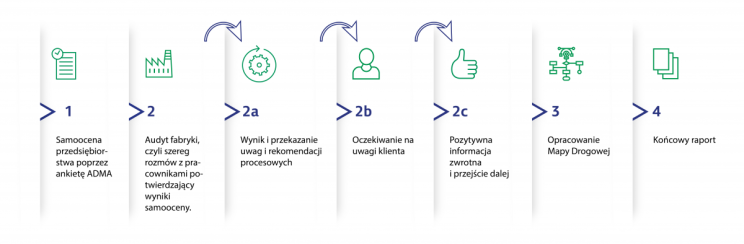
Od czego zacząć tworzenie mapy drogowej
Na początku konieczne jest dokonanie audytu firmy, określenie miejsca, w którym się jest, jeśli chodzi o cyfrową transformację, wyznaczenie najważniejszych wskaźników z punktu widzenia Przemysłu 4.0. W firmie Supron 3 audyt rozpoczął się od wypełnienia przez zarząd szczegółowych ankiet dostarczonych przez firmę ASTOR, ankieta pozwoliła oszacować stan gotowości przedsiębiorstwa na zmiany, jego zaawansowania technologicznego, ale też roli jaką w organizacji odgrywają nowe technologie, jak ich wykorzystanie przekłada się na zaspokajanie potrzeb klientów.
Drugi etap audytu polegał na pojawieniu się w firmie ekspertów nie tylko z firmy ASTOR, którzy na miejscu zbadali stan techniczny linii produkcyjnych i infrastruktury oraz organizację zadań.
Zebrane obserwacje wymagały następnie omówienia. W siedzibie firmy ASTOR odbyły się dwudniowe warsztaty, których celem było podsumowanie i opracowanie wniosków. Pierwszy dzień miał charakter pokazowy. Przedstawiciele firmy Supron 3 mieli okazję zapoznać się z rozmaitymi przykładami implementacji cyfrowych rozwiązań z obszaru Przemysłu 4.0 w różnych konfiguracjach produkcyjnych.
Drugi dzień był już stricte warsztatowy. W spotkaniu wzięło udział najwyższe kierownictwo firmy Supron 3 ze wszystkich działów. Założenie było takie, że uczestnicy nie dostają prostych wskazówek, a w toku rozmowy, w sekwencji pytań i odpowiedzi są naprowadzani na pewne rozwiązania. Chodziło o to, aby za ostateczne decyzje odpowiedzialni byli oni sami.
Spotkanie okazało się bardzo stymulujące i owocne. Jego rezultatem było wyznaczenie kierunku transformacji i pierwszych działań skoncentrowanych wokół montażu automatycznego centrum gnącego, które znacznie ułatwia proces produkcji szaf ochronnych. Centrum gnące to skomplikowana i zautomatyzowana maszyna, która pozwala na wykonanie całego korpusu szafy na jednym urządzeniu. Pozwala zrezygnować z kilku pras krawędziowych, które dotąd realizowały to zadanie, a były obsługiwane przez dwóch trzech operatorów.
Automatyczne centrum gnące sterowane jest przez jednego pracownika, choć wymaga większego zaangażowania działu projektowego. Wprowadzenie tego rozwiązania pozwala skrócić proces produkcyjny, ale też zapewnienia niezwykle pożądaną obecnie elastyczność umożliwiającą szybkie odpowiadanie na zmieniające się potrzeby rynku.
Jak wygląda praca nad mapą drogową
Zdobycie dofinansowania pozwalającego zrealizować ten projekt to jeden z celów podjętych działań, ale w toku prac nad mapą drogową zarząd zdał sobie sprawę, że nawet jeśli dofinansowania nie będzie, transformacji nie można zatrzymywać. Centrum gnące i tak zostanie zakupione, a mapa drogowa posłuży do realizacji dalszych działań modernizacyjnych.
Sama mapa już powstała, jest kilkusetstronicowym dokumentem, który dokładnie wymienia sekwencję zaplanowanych działań wskazując jednocześnie zadania priorytetowe. To kompleksowe opracowanie, które skupia się nie tylko na aspektach technicznych, ale też organizacyjnych i kompetencyjnych.
Prace nad dokumentem trwały sześć miesięcy i zaangażowały przedstawicieli kierownictwa ze wszystkich pionów: przede wszystkim z działu produkcji i montażu, ale też z IT, zaopatrzenia i sprzedaży, czy z działu projektowego. Przy tym udało się tak zorganizować prace nad mapą, by nie ucierpiała bieżąca działalność firmy mimo zaangażowania w projekt wszystkich najważniejszych interesariuszy w firmie.
Udało się też uniknąć impasów w całym procesie. Oczywiście pojawiało się zmęczenie, ale generalnie prace toczyły się sprawnie. Gdy okazywało się, że jest jakieś wąskie gardło, np. że jest tylko jeden zatrudniony informatyk, firma uruchamiała proces rekrutacyjny i zwiększała ich liczbę do trzech.
Najważniejsze etapy tworzenia mapy drogowej:
- Ankieta
- Audyt prowadzony przez ekspertów zewnętrznych
- Spotkania warsztatowe
- Przygotowanie dokumentu
- Realizacja zaplanowanych inwestycji i implementacja rozwiązań
- Ciągła refleksja na temat kondycji firmy w oparciu o mapę drogową
Jakie korzyści daje mapa drogowa
Dzięki powszechnemu zaangażowaniu załogi, wartość mapy drogowej uwidacznia się na wielu płaszczyznach. Dla właścicieli i zarządu dokument ma znaczenie strategiczne. Pozwala dostrzec najważniejsze wyzwania stojące przed firmą w nadchodzących latach i zbudować założenia strategiczne w horyzoncie 5-10 lat. Dodatkowa wartość wynika z faktu, że w zarządzie firmy są osoby spoza branży. Przestudiowanie dokumentu pozwala im lepiej ją zrozumieć i wejść w głąb potrzeb samej organizacji.
Z drugiej strony mapa drogowa jest niezwykle wysoko oceniana przez kierowników operacyjnych, bo wskazuje najważniejsze zadania dla ich działów, ale umieszcza je w kontekście całej organizacji i jej celów nadrzędnych.
Pracownikom niższych szczebli dokument porządkuje i upraszcza proces produkcji. Sprawia też, że praca jest mniej frustrująca.
Osoby ze wszystkich szczebli hierarchii widzą w dokumencie narzędzie pozwalające skalować cyfrową transformację w całej organizacji, a przez to przyczyniać się do jej rozwoju.
Założenie jest takie, że będzie to dokument aktywny, szeroko udostępniany w organizacji, przez co będzie przekładał się na praktyczne działania każdego pionu.
Mapa drogowa a zasoby ludzkie i kompetencje
Olbrzymie zaangażowanie załogi w projekt tworzenia mapy drogowej uruchomiło duże pokłady motywacyjne. Pojawiło się poczucie sprawczości i pozytywna energia. Prace uświadomiły jednak także, że istnieją pewne luki kompetencyjne, które należy wypełnić. W rezultacie, obecnie firma ma zaplanowane na najbliższy rok liczne szkolenia, dotyczące zarządzania czy lean management.
Kursy, które do tej pory odbywały się w firmie miały charakter techniczny. Dotyczyły najczęściej obsługi konkretnych maszyn. Praca nad mapą drogową uświadomiła zarządowi, że konieczne jest także budowanie umiejętności zarządczych i tzw. kompetencji miękkich, w tym w obszarze rozwoju osobistego. Priorytetem są też kompetencje cyfrowe.
Wcześniej to zarząd był inicjatorem szkoleń, obecnie sami kierownicy widzą potrzebę rozwoju, podnoszenia kwalifikacji zarówno swoich jak i podwładnych by mogli delegować zadania na najniższy szczebel. Wyzwaniem jest wyrównanie poziomu wszystkich tych zdolności w całej organizacji, zwłaszcza w związku z dużą różnorodnością załogi złożonej zarówno z osób 50 plus, jak i dwudziestolatków. W obliczu tego wyzwania, firma stanęła przed koniecznością stworzenia działu administracyjnego, który zajmowałby się kwestiami zasobów ludzkich.
Wcześniej istniał w firmie dział kadr, ale jego zadania koncentrowały się wokół tzw. twardego HR: zapoznawanie pracowników z regulacjami wynikającymi z prawa pracy, wypełnianie formularzy. Większy nacisk na kompetencje miękkie i rozwój sprawił, że dział HR został w firmie Supron 3 przebudowany i wzmocniony. Praca nad mapą drogową pokazała kierownictwu, że te wszystkie obszary są bardzo ważne i kapitał ludzki wymaga stałego rozwijania i troski.
Lista zadań na przyszłość
Przy okazji pracy nad mapą drogową powstała długa lista zadań, które mają być zrealizowane w przyszłości. Firma ma świadomość, że znalazła się w momencie przełomu, że przechodzi od chaotycznych reaktywnych działań do realizacji dobrze zaplanowanej i przemyślanej strategii cyfryzacji. Co ciekawe, w firmie Supron 3, te działania zbiegają się ze zmianą pokoleniową. Od trzech lat w zarządzie firmy zasiadają wyłącznie przedstawiciele młodego pokolenia. To oznacza nie tylko większy nacisk na procesy modernizacyjne, ale też zmianę stylu zarządzania, z autorytatywnego na bardziej rozproszony. W sytuacjach problematycznych członkowie zespołów spotykają się, dyskutują i wspólnie wypracowują rozwiązania. Zarząd wychodzi z założenia, że „nie ma głupich pytań”, a z dyskusji zawsze wychodzi coś pozytywnego.