Euromap 67 – communication interface for industrial robots cooperating with injection molding machines
In this article you will learn:
- What Euromap 67 standarts is and how it works
- Why you should use Euromap67,
- Why it is worth using 6-axis robots with injection molding machines.
Euromap 67 is a reliable communication standard that enables efficient, smooth, and safe integration of a robot with an injection molding machine.
Tendency to increase efficiency, improving product quality, and enhancing production process flexibility means that companies are increasingly adopting advanced technological solutions. One of the simplest and most effective methods of boosting productivity is process automation through robotics.
In the case of handling the injection molding process, robots not only unload the machine, but also perform additional tasks such as loading inserts, removing sprues, sorting, post-processing, and quality control.
To integrate a robot with injection molding machine effectively and safely, a reliable communication standard between the devices is essential. That standard is Euromap 67. It is standardized communication protocol develop by EUROMAP – the Europe’s Association for plastics and rubber machinery manufacturers. Its main purpose is to define electrical interface between injection molding machines and handling devices such as an industrial robots, to ensure mutual communication This protocol simplifies the integrations of robots that performs tasks such as unloading finished molded parts from the injection mold.
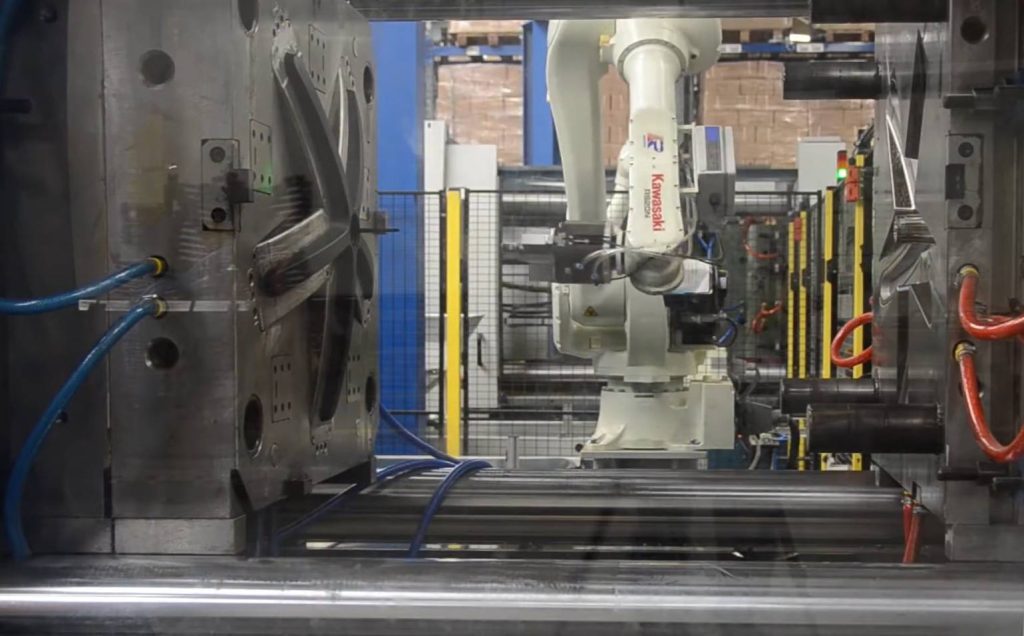
The principle of how the Euromap 67 protocol works
The Euromap67 protocole defines several layers of communication. At the physical layer, it specify the type of connectors, plugs, pin layouts and voltage levels of the system. On the logical and communication layers, signal handling and messaging have also been standardized. Each pin is assigned to dedicated signal and particular machine state or action. To initiate an action, such as the robot collecting parts, a specific sequence of signals must be send and receive. In case where confirmation is not received, the action will not be carried out. Most output signal have corresponding input. Thanks to that robot’s operation with injection molding machines with Euromap67 is fully coordinated.
For example before robot takes the detail out from mold, it must ensure that the injection molding machine has complete the cycle and the mold open. To do this, the robot sends the signal ‘B3: Enable ejector back’ as a request to retract the ejector. The Machine respond with “ZB3: Ejector back position´ only when ejector has actually moved to its starts position. Signal “B3” must remain active from the moment it is sent until the confirmation “ZB3” is received. A similar process applies to “B4 – Enable ejector forward” and its confirmation “ZB4”. This ensures deterministic synchronization—the robot knows exactly when the molding machine has completed a movement, minimizing delays and avoiding collisions.
Thanks to the use of digital signals for machine state confirmations, communication is instantaneous, and there are no issues with data packet loss. If communication between the devices fails, diagnostics are very straightforward due to the protocol’s low complexity.
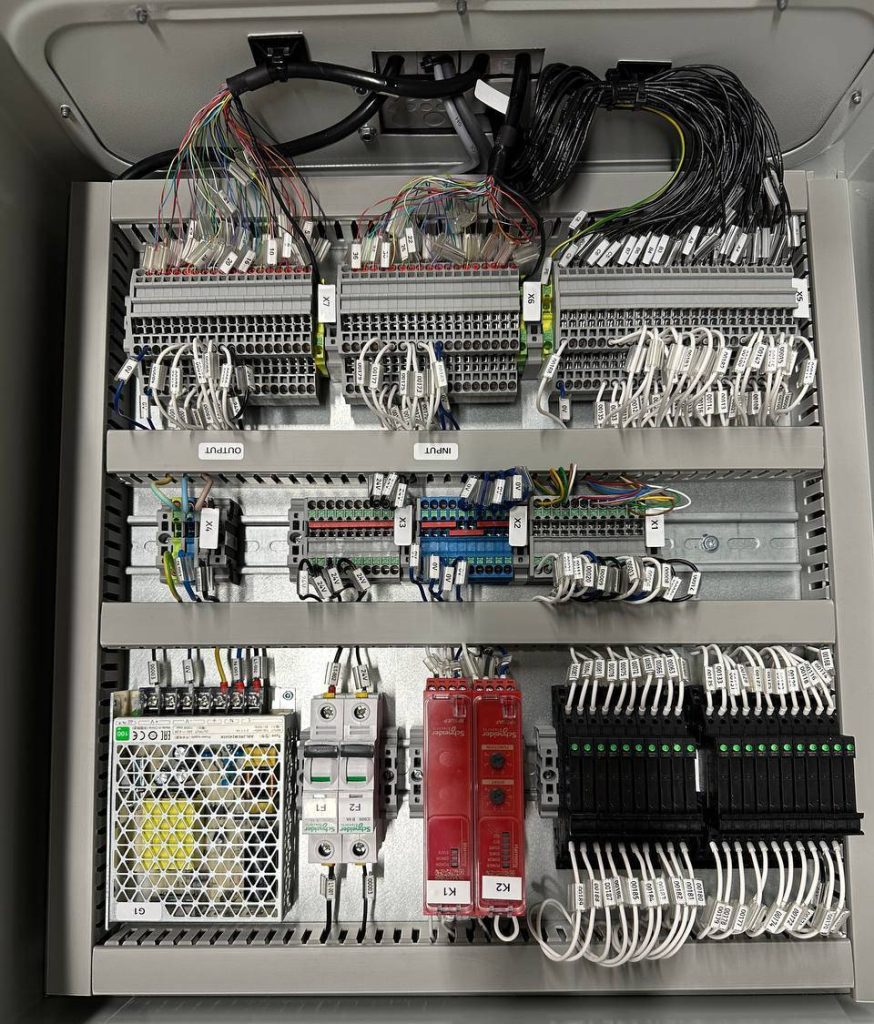
Why is it worth to use Euromap67?
Thanks to this protocol, a robot and any injection molding machine can start working together in a practically plug & play manner, without the need to develop a custom wiring scheme or control logic. Once the cables between the two machines are connected, both devices immediately recognize each other’s states. Safety signals, mold opening, ejector movements, or injection start are automatically transmitted between the devices. This significantly reduces both the time and cost of deploying a robot to operate with an injection molding machine.
The Euromap 67 protocol standardizes communication and data exchange between various devices within a production system. It defines standard handshake signals (e.g., door status, robot in operation, ejector position), which are consistently transmitted between the robot and the injection molding machine. This standardization ensures that both the robot and the molding machine understand each other’s status and can effectively coordinate their actions. Standardized communication enables reliable and predictable interactions, which is critical for smooth operation of the automated cell and for preventing errors or collisions.
For instance, if the robot needs to know when the mold is open before it can enter, Euromap 67 provides a standardized “Mold Open” signal that is recognized by both the injection molding machine and the robot, preventing the robot from attempting to enter too early.
Thanks to simplified integration and standardized communication, automated systems based on Euromap 67 are characterized by increased efficiency and reliability. Streamlining the integration process and unifying communication leads to shorter setup times and reduced downtime. Reliable data exchange ensures that the robot performs its tasks at the correct moment in the injection molding cycle, thereby optimizing the entire production process.
By simplifying integration and enhancing communication reliability, Euromap 67 directly contributes to increased productivity and reduced operating costs in manufacturing. Faster setup means production can begin sooner, and dependable communication minimizes the risk of errors that could lead to downtime or the production of defective parts, which ultimately improves overall efficiency.
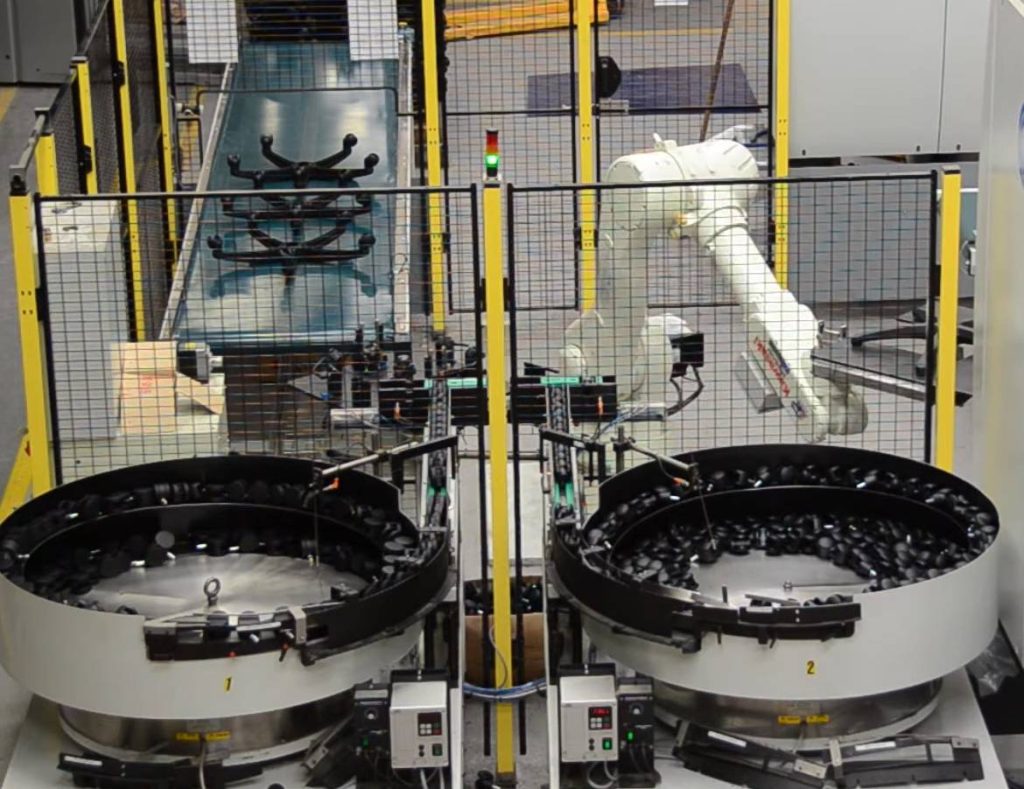
Why it is worth using 6-axis robots with injection molding machines?
Cartesian robots are commonly used to operate injection molding machines and perform well when the task is simply to remove the finished product. In the case of more complex molds or when additional tasks are assigned to the robot during the injection molding machine operation, they may prove insufficient.
What are the advantages of using a 6-axis robot?
Power
Thanks to powerful and compact drives, a 6-exis robot robot is able to generate high pulling force, allowing it to handle heavy molded parts and reduce the number of ejector cores in the mold. The robot can cope with additional resistance when removing the product from the mold.
Multi-axis manipulation ability
Six axes mean six degrees of freedom. Thanks to that, 6-axis robot is able to extract elements with very complex shapes. It can also perform additional operations, such as placing inserts into the cavities.
Simplification of injection mold design
Thanks to mobility of the 6-axis robot, design simpler molds with fewer moving parts is possible.
Ability to perform additional tasks
The agility of 6-axis robots means they can be used for additional tasks after removing molded parts from the mold. These include cutting off sprues, deburring products, conducting quality control, labeling or packing.
Space savings
In the case of Kawasaki Robotics RS series robots, the compact design may allow them to take up less space than traditional Cartesian robots. A small footprint and the ability of the arm to fold back while retreating from the machine mean the robot does not require much space above or behind itself to freely extract elements from the injection molding machine. This allows for denser machine placement, improving production efficiency.
Summary, conclusions and future
In summary the Euromap67 communication protocol combine with 6-axis industrial robots, offers a number of key advantages and finds broad application in the injection molding industry. The most important benefits include:
- Simplification of the robot-machine integration process,
- Standardization of communication and data exchange,
- Increased efficiency and reliability of automated systems,
- Support for safety and redundancy functions.
In addition to the Euromap 67 protocol, there are other versions and standards within the Euromap family. Euromap 12 is an older version of the electrical interface, featuring fewer connections (32 compared to 50 in Euromap 67) and a single-channel safety circuit. With appropriate adapters, devices operating under different standards can be connected and work together using the older Euromap 12 standard.
Future developments in communication between robots and machines in the industry point toward using more advanced standards that provide access to more data. The Euromap 79 standard, based on OPC UA, has already been developed and offers more extensive data exchange capabilities. Due to the non-deterministic nature of the OPC UA protocol, safety signals remain in digital form; their implementation and integration are described in Euromap 81.
This development responds to the industry’s demand for collecting more data to optimize production. The OPC UA based solution fits into the IIoT trend, which is a key part of Industry 4.0. The ability to collect data allows it to be used in higher level supervisory systems such as SCADA, and further used to optimize future production batches.
ASTOR specializes in delivering comprehensive industrial automation and robotics systems. Feel free to contact us if you are looking for a partner in connecting the Euromap 67 protocol with an industrial robot.