WIŚNIOWSKI – digital individualisation in the factory of the future
Goals:
• Improved production efficiency
• Improved quality of the production processes
• Enhanced safety for operators
Benefits:
• Reduced lead-time
• Tripled productivity of the robotic door welding process
• Perfect weld quality thanks to robotised welding
“We automatise those processes whose robotisation brings real benefits. Using modern technologies, we improve the quality of production processes and, importantly, we increase the safety of operators’ work. Now, we achieve excellent weld quality and high productivity.” said Maciej Socha, Director of Fencing Systems and Corrosion Protection Department, WIŚNIOWSKI
About the company
WIŚNIOWSKI has nearly 30 years of experience in the construction industry. Investment in new technologies, improving quality and extending the offer, as well as innovativeness and entering new markets are the features which have made it a leader in its industry.WIŚNIOWSKI is a proof that Polish companies can be successful not only in domestic markets but also foreign ones. The WIŚNIOWSKI brand products are sold in 2500 outlets in Europe. Currently, the company employs nearly 1700 people.
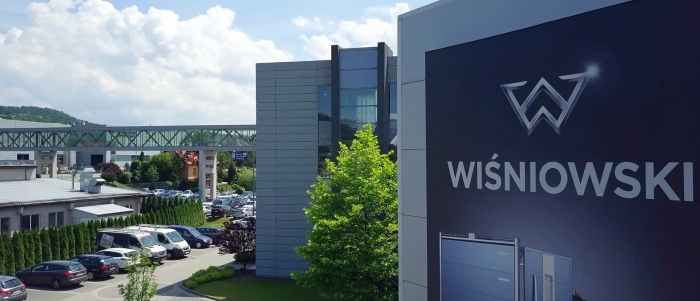
WIŚNIOWSKI carries out production based on an Integrated
Quality Management System. All components of WIŚNIOWSKI industrial fences and gates are laser cut, robot welded and subjectedto the best anticorrosive protection methods in the form of galvanising and powder coating. Zinc coating obtained by immersing a chemically cleaned construction in a liquid zinc protects elements of the WIŚNIOWSKI fences against corrosion for decades. The aesthetic and unique look of the final product is additionally provided by polyester protective coating in any of over 200 RAL colours.
The smartCONNECTED idea from the WIŚNIOWSKI brand is the next stage of technological revolution. Just as several years ago automatic gates revolutionised the market of garage and fencing gates, now their introduction to the Internet of Things will improve the standard of living.
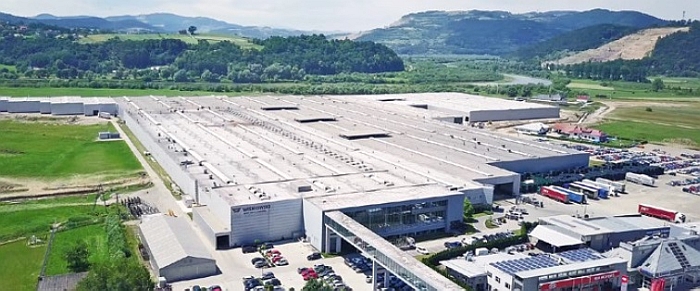
Challenges
The concept of robotised welding of fencing systems, which are one of the key product groups in the WIŚNIOWSKI company’s offer, emerged in the Management Board’s plans several years ago. Due to the wide range of types and sizes of manufactured fences, automation of this process at WIŚNIOWSKI was a very difficult undertaking that was implemented in two stages.
The first stage was carried out in 2014/2015, when the first station for robotic welding of fencing systems for individual customers was completed. In 2016/2017, together with ASTOR and two integrators: Zelkon and Acars, phase two was implemented – automation of welding industrial fencing systems and robotic cleaning of mesh panels.
In the welding automation process, ASTOR delivered state-ofthe-art robots and control systems as well as added value: optimisation of a larger process – order flow and execution, supporting the
WIŚNIOWSKI’s comprehensive customer service strategy.
Project implementation
Orders are automated as soon as they are placed at the point of sale. The software developed and implemented by the ACARS integrator ensures a smooth order flow: orders stored in the ERP system
are automatically converted into a software for industrial robots – the system autoconfigures itself for the welding process of the product according to the order placed in the system. This makes it possible to carry out individualised production on a mass scale.
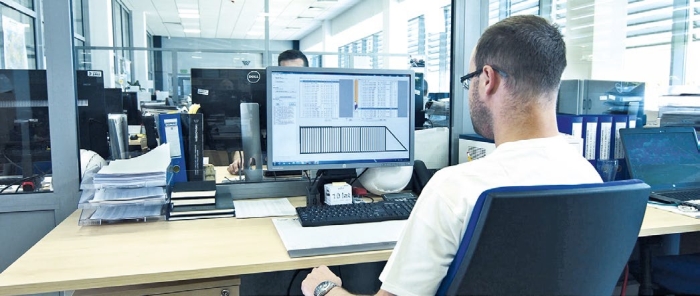
The ASTOR Green Welding station, built by integrators Zelkon and ACARS, operates using two Kawasaki palletizing robot industrial welding robots and the Fronius welding equipment. The robots move on a 17-metre track, which makes it possible to weld gates of large size. The robots are mounted on column-and-boom manipulators – this solution allows to optimise performance and maximise the working range of the robots.
“The achieved degree of automation enables full process control and high manufacturing flexibility. Thanks to the integration of the ERP system data with the production system, the time of preparing a new product is significantly shorter. The solution, based on state-of-the-art Kawasaki industrial robots, supports the implementation of the Customer’s business objectives and is in line with the idea of Industry 4.0.”– Adam Pajda, Project Manager, Control systems and robotics specialist, ASTOR.
The robots also work with the ASTOR Green Welding positioners. Using two similar turntables makes the workstations very versatile – the robots can simultaneously weld one object using the larger positioner or work independently on both workstations, manufacturing two gates at the same time.
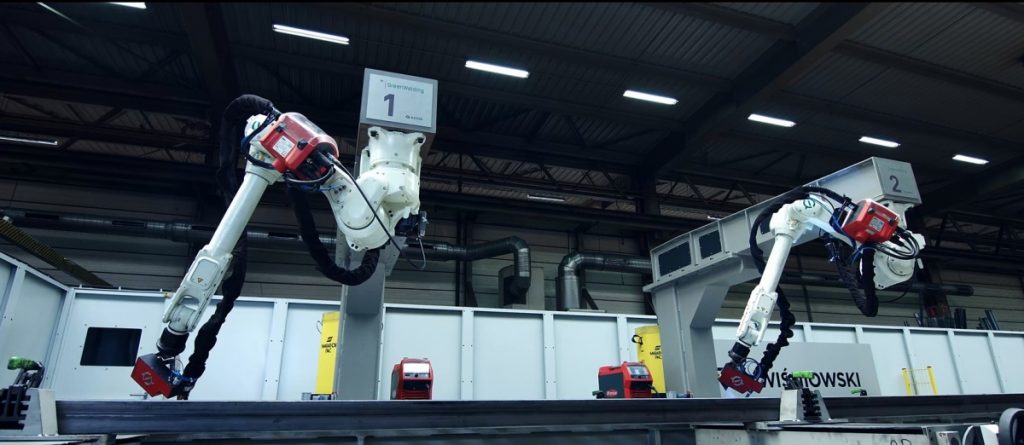
The modularity of the ASTOR positioners allows the system to be further expanded or modified to meet new production plant needs.
“The implemented solution is an incredible convenience for operators! What does an operator need to know? First of all, they have to know the sequence of the system, assemble a product with the right elements in the right order on the machine, switch on the button and control the welding process” – summarises Mariusz Leśniak, robotic welding line operator at WIŚNIOWSKI.
An additional benefit for the operators of the station is the use of automatically controlled basins under the turntables, which are recessed into the floor when the gate rotates and are levelled with the floor during assembly and disassembly of the gate by the operators. This solution simplifies work and ensures the safety of employees. The user interface is the Astraada panel computer equipped with the Wonderware InTouch software which, apart from being the tool controlling the ASTOR Green Welding system, acts as a link between the WIŚNIOWSKI internal systems and the workstation software.
The brain of the entire system is GE Automation&Controls’ flagship PACSystems RX3i controller. It provides continuous communication between the system components and controls its operation.
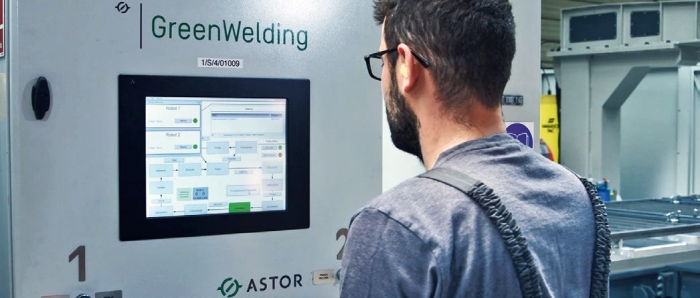
Benefits
Significant time savings have also been achieved in the order fulfilment process, and the work of programmers and welding station operators has been optimised. The robots ensure repeatable welding quality. Welds are exceptionally aesthetic and perfectly prepared for further production stages. The use of robots makes it possible to improve operators’ professional skills, also thanks to training delivered by ASTOR.
Implementation of the system made it possible to systematise the production process – from production planning, through its execution to the quality of the final product. This process has become more predictable and accurate. The system has also made it possible to shorten the execution time of serial orders – mainly in the context of export orders. The system was introduced in those locations where it was necessary to perform repetitive and monotonous activities and where working conditions were onerous for people.
The robotisation of production ensured an increase in productivity, made it possible to improve quality and stabilise technological processes, and additionally reduced the time of performing operations. The introduction of this system also provided the possibility of optimal management of the production hall space. Moreover, automation allowed for maintaining the dynamics and fluency of production, as well as for manufacturing according to individual orders.
The technological revolution we are witnessing is fundamentally changing the way we live and work. In a business context, this means that customer expectations are constantly rising. Nowadays, it is no longer enough to have a product of excellent quality. It must be designed in such a way that it best meets the individual needs of the recipient.