Treści
Jak optymalizować ciągłe procesy produkcyjne dzięki cyfrowym bliźniakom
Jak optymalizować ciągłe procesy produkcyjne dzięki cyfrowym bliźniakom
Jak za pomocą cyfrowych bliźniaków wprowadzać w życie strategie optymalizacji aktywów? W ciągłych procesach produkcyjnych, możemy poprawiać zwrot na aktywach operacyjnych z wykorzystaniem kilku rodzajów digital twins – od dynamicznych symulatorów procesów, poprzez narzędzia do implementacji strategii risk-based maintenance do rozwiązań optymalizujących zużycie mediów produkcyjnych. Obszar risk-based maintenance proponuje największe potencjalne korzyści i łatwość zastosowania cyfrowych bliźniaków.
Inwestycje w instalacje technologiczne w energetyce, przemyśle rafineryjnym, chemicznym, gazowym, wodociągowym, czasem także w przemyśle spożywczym, mają swoją specyfikę, zależną silnie od nakładów inwestycyjnych, wymaganego poziomu bezpieczeństwa, dostępności produkcji oraz długiego oczekiwanego cyklu życia. Wartość tych aktywów niejednokrotnie oscyluje w granicach od kilkuset milionów do kilku miliardów złotych.
Dlatego warto na nie spojrzeć strategicznie i zastanowić się:
- Jakim wskaźnikiem mierzyć efektywność wykorzystania takich aktywów / instalacji?
- Jak za pomocą cyfrowych bliźniaków wprowadzać w życie strategie optymalizacji aktywów?
Zwrot na aktywach operacyjnych
Praktycznym wskaźnikiem oceny efektywności pracy takich instalacji, może być zwrot na aktywach operacyjnych (Return on Operating Assets, ROOA). Odpowiada on na pytanie, ile zysku netto generuje firma z aktywów zaangażowanych w produkcję, np. maszyn/instalacji, zapasów oraz licencji oprogramowania wykorzystywanego do zarządzania procesami produkcji. Wskaźnik nie jest popularny w księgowości, natomiast może dać dużą wartość w controllingu strategicznym.
Przykładowo, jeśli dostępność kluczowej instalacji spada ze względu na nieplanowane awarie, to spada wydajność produkcji i prawdopodobnie także sprzedaż i zysk wypracowany przez tę instalację. Dodatkowo rosną koszty napraw. Czyli wartość wskaźnika ROOA się pogarsza. Z drugiej strony, jeżeli potrafimy zoptymalizować pracę instalacji, tak, żeby zużywała mniej energii, albo osiągała maksymalne wydajności w czasie, gdy taryfa jest najtańsza, to obniżamy TKW (techniczny koszt wytworzenia) i jednocześnie podnosimy zysk netto oraz ROOA.
Cyfrowy bliźniak a zwrot na aktywach operacyjnych (ROOA)
W ciągłych procesach produkcyjnych, możemy poprawiać zwrot na aktywach operacyjnych z wykorzystaniem kilku rodzajów cyfrowych bliźniaków. W zależności od celu biznesowego mogą być to: dynamiczne symulatory procesów, narzędzia do implementacji strategii risk-based maintenance, narzędzia do projektowania i uruchamiania instalacji oraz cyfrowe narzędzia optymalizujące zużycie mediów produkcyjnych. Zostało to przedstawione na poniższym rysunku. W tym opracowaniu skupimy się na obszarze Risk-based maintenance, gdyż naszym zdaniem dostępność technologii, łatwość zastosowania cyfrowych bliźniaków i potencjalne korzyści biznesowe w tym obszarze wymagają nadania mu wysokiego priorytetu.
Strategiczna optymalizacja wykorzystania aktywów, czyli od gaszenia pożarów do risk-based maintenance
W procesie zarządzania kluczowymi instalacjami, utrzymanie ich wysokiej dostępności jest ważne zarówno dla ich bezpieczeństwa, jak i rentowności całego biznesu. Dlatego warto budować dla tych aktywów zaawansowane strategie utrzymania ruchu. Strategie te można opisać poziomami dojrzałości, gdzie najniższy poziom to klasyczne „gaszenie pożarów” (reactive maintenance), a poziom piąty, najwyższy, to utrzymanie ruchu oparte na zarządzaniu ryzykiem (risk-based maintenance/ prescriptive maintenance). Na poziomie najwyższym budujemy model oceny i kategoryzacji ryzyk oraz plany ich mitygacji, czyli jak powinniśmy się zachować, jeśli w maszynie zacznie się psuć konkretna część. Czy lepsze w tym momencie będzie zatrzymanie instalacji czy ciągłe monitorowanie wybranych parametrów i warunkowa kontynuacja produkcji? Takie podejście wymaga integracji podejścia technicznego z efektem finansowym podejmowanych decyzji. Wszystkie poziomy dojrzałości strategii utrzymania ruchu zostały zaprezentowane w poniższej tabeli.
Oparte na zarządzaniu ryzykiem, czyli optymalne utrzymanie ruchu, pozwala na znalezienie punktu, w którym będzie zapewniona wysoka dostępność i bezpieczeństwo instalacji, a z drugiej koszty całkowite koszty akcji serwisowych i części zamiennych nie będą przewymiarowane. Podejście zostało zobrazowane na poniższym diagramie.
Rozwiązania wspierające strategię risk-based maintenance mają następujące funkcjonalności:
- RCM (Reliability Centered Maintenance) zgodne z filozofią FMECA (Failure Mode Effetcs and Criticality Analysis),
- RCA (Spare Part Optimization and Root Cause Analysis),
- Biblioteki Asset Strategy,
- Dashboardy i raporty menedżerskie.
W jaki sposób działa taki system?
W pierwszym etapie kluczowe jest zdefiniowanie celów biznesowych dla utrzymania ruchu w wybranej instalacji. W skrócie: budujemy macierz prawdopodobieństw i konsekwencji wystąpienia awarii. Następnie definiujemy, jak dane awarie wpływają na funkcjonalność całej instalacji i oceniamy poziom krytyczności danej awarii, czyli jej wpływ na konieczność zatrzymania instalacji oraz jej bezpieczeństwo pracy. Następnie w cyklu PDCA (Plan Do Check Act) definiujemy scenariusze działań w momencie wystąpienia danego typu awarii. Diagram opisujący działanie przykładowego systemu optymalizacji zasobów produkcyjnych został zaprezentowany poniżej.
W normalnym użytkowaniu system zarządzania aktywami przewiduje następujące scenariusze użycia:
- Symulacja wybranych strategii utrzymania ruchu, która pozwala wyliczyć biznesowe i techniczne efekty decyzji serwisowych i eksportować te strategie do systemów planowania i realizacji akcji serwisowych,
- Kompleksowa analiza przyczynowo-skutkowa (RCA, root-cause analysis) dla zarejestrowanych incydentów i awarii, definiowanie reguł zachowań i rozwiązań problemów w bazie wiedzy,
- Wykorzystanie bibliotek strategii działań i modeli dla różnych aktywów, m.in. pomp, sprężarek, kotłów, turbin gazowych, turbin parowych, zaworów, generatorów, dmuchaw oraz nagrzewnic powietrza.
Przykładem zastosowania może być monitoring predykcyjny i zarządzanie ryzykiem w pracy pieca obrotowego do produkcji cementu. W tego typu instalacji, praca łożysk jest monitorowana przez system predykcyjny, który przewiduje, jak powinien wyglądać sygnał wibracji. Ten sygnał referencyjny jest porównywany z aktualnym. Duża różnica pomiędzy nimi jest traktowana jako anomalia.
Dzięki porównaniu dwóch sygnałów wykryto niestandardowe wibracje. System rozpoznał je jako anomalię, ale korzystając z macierzy oceny ryzyka ustalił, że ryzyko związane z kontynuacją pracy do czasu zakończenia partii produkcyjnej jest akceptowalne. Serwis i wymiana łożyska zostały przeprowadzone w późniejszym terminie. Dzięki temu firma uniknęła straty na poziomie 7 000 ton produktu gotowego, a po zakończeniu produkcji wymieniono łożysko o wartości 3 tys. USD. Łatwo oszacować szybkość zwrotu z tej inwestycji.
Dowiedz się więcej
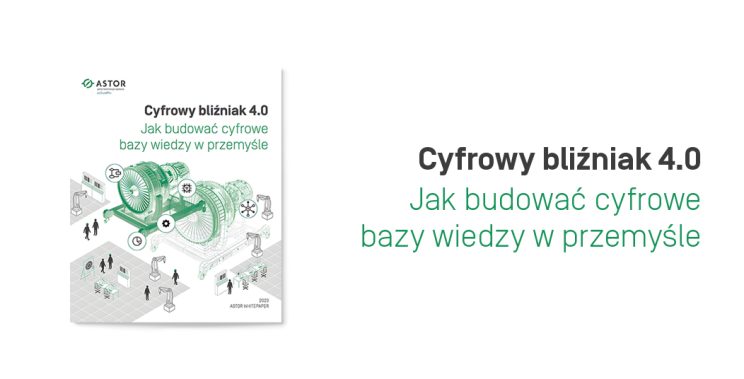
Dowiedz się więcej o cyfrowym bliźniaku w nowej publikacji „Cyfrowy bliźniak 4.0. Jak budować cyfrowe bazy wiedzy w przemyśle.„