Precision motion control. What are servo drives?
From this article you will learn:
- what a servo drive is and what it consists of,
- what are the types of encoders and how they differ,
- what to pay attention to when selecting wiring for servo drives.
Industrial automation is becoming more and more precise. There are increasing requirements for product quality on the one hand, and for the performance and reliability of production equipment on the other. To meet these requirements, it is very important that the machines used have the right characteristics. The needed quality and precision can be provided by servo drives. By reading this article you will learn basic information about servo drives: what they are, what they consist of and what are the differences between them.
What is a servo drive?
Servo drives are devices used to precisely realize the movement of components of devices and machines, taking into account all its parameters. These are drive modules responsible, among other things, for moving robot arms and axes of CNC machines, but not only. Servo drives work very accurately and have high efficiency, so they can be used in any machine where efficiency and high precision are needed.
It may seem that a servo drive is simply a motor. However, this is a gross oversimplification, as it is actually a device consisting of such components as a servo motor, servo amplifier, encoder cables and power cables. I will briefly discuss each of these components below.
What is a servo drive and what is a servomechanism?
To begin with, I would like to dispel common doubts and discuss the differences between a servo and a servo drive. These two terms are often confused with each other. A servo drive is an actuator system consisting of:
- a motor,
- servo amplifier that houses the servo controller,
- encoder cables,
- and power cables.
The servo drive is part of a larger whole, the servomechanism. In addition to this, it includes a gearbox and, optionally, if needed, a PLC that can perform additional advanced functions, such as input and output control, axis synchronization or PLCopen standards. When the controller is installed, the implementation of the feedback loop is often transferred from the servo amplifier precisely to the PLC.
Each of the components of the servo amplifier plays an important role in the operation of the machine, so it is very important to select them properly when configuring your own servo amplifier.
Servo motor
The basic component included in the servo drive is the servomotor. Technically speaking, it is a classic AC asynchronous motor with an integrated encoder. The servomotor is the executive element of the entire servo drive. It is responsible for the movement of a given part of the machine. It is connected to the servo amplifier responsible for generating the motor's set values. This device is powered by alternating current.
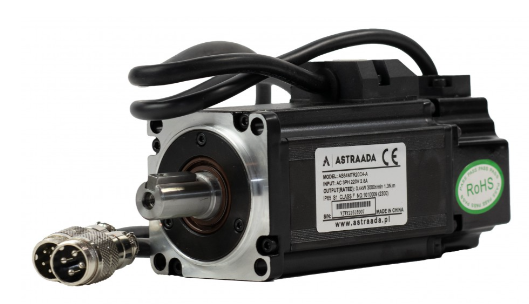
Differences between incremental and absolute encoders in servo motors
Encoders are devices that change rotary motion into electrical signals. They provide precise information about the current state of the motor shaft - its angular position, direction of rotation and the number of revolutions made.
In absolute encoders, the output signal is generated in analog form. Each position on the encoder disc is equipped with a code uniquely identifying it. This results in each angular position of the shaft having its own code value on the output. The absolute encoder disc also has an additional incremental path, so that a digital signal can also be generated at the output. The advantage of this type of device is that the position of the servo motor can be read when the power is turned off. An absolute encoder measures the relative position of the servo motor.
An incremental encoder generates pulses at the output that correspond to rotational motion. It has a certain resolution, which tells us how many output pulses correspond to a given angular displacement. Naturally, the higher the resolution, the higher the measurement accuracy. In the case of an incremental encoder, it is not possible to read its current position after losing power.
Servo amplifier
A servo amplifier is a device that controls a motor using data from an encoder. It is used to make a given number of revolutions, change the position of the shaft by a specific angle or change its speed. It is the I/O terminal and STO connector that can be communicated with via appropriate communication protocols such as Modbus RTU. In simple terms, a servo amplifier for a servo motor is what an inverter is for a simple asynchronous AC motor.
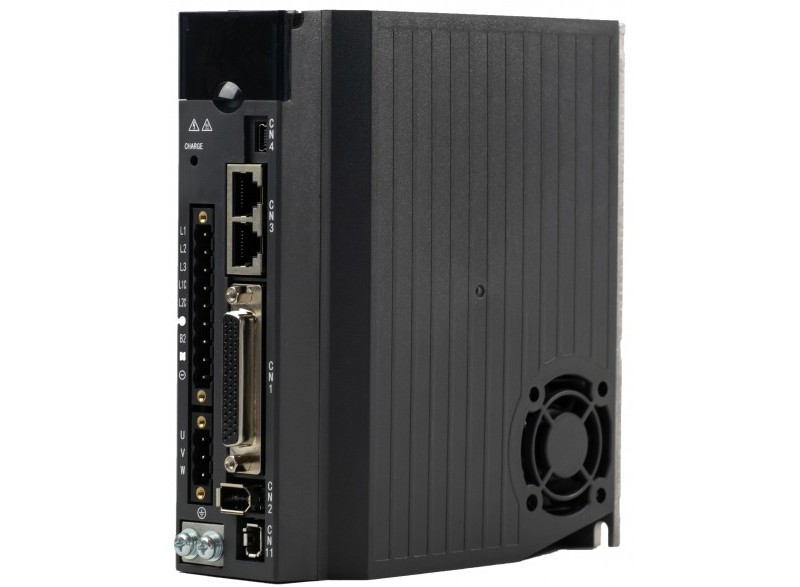
You may also encounter the term "servo controller" when referring to a servo amplifier. It is not quite correct, because the servo controller is a component of the servo amplifier. The servo controller itself is responsible for tasking control signals, which then need amplification. Hence, it is the device that transmits control signals and then amplifies them by feeding them directly to the servo motors that is called a servo amplifier.
The servo amplifier is not always the main master unit in a servo motor. Often it works in conjunction with a PLC, and it is the PLC that issues specific commands to the servo amplifier, which translates them into the rotation of the servo motor at a given speed and position. The servo amplifier and the PLC can communicate with each other through communication protocols such as EtherCAT, Modbus, Profinet, Profibus, etc., but also through simple signals sent from the PLC's I/O terminal.
Wiring
For each servo drive, we need to have two types of cables - power and encoder cables.
The cables should be properly selected according to the parameters of our device: supply voltage - 230 V or 400 V, motor power ora type of encoder - incremental or absolute. It is also worth considering the use of cables with battery backup.
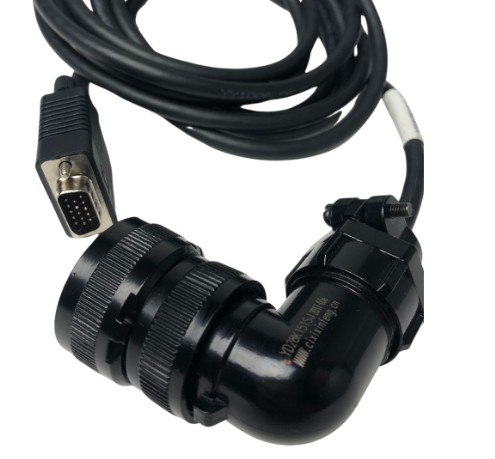
When selecting cables, you need to pay attention to the fact that they are flexible and shielded. What is the difference between the two? Shielded cables protect against electromagnetic interference resulting from the pulsation of the flowing current in the cable. Flexible cable, on the other hand - thanks to a special rubber sheath - is flexible and soft, yet durable. This makes it easier to hide it in the closet so that it does not get in the way.
Differences between servo and stepper motor.
Let's start by explaining the principle of the stepper motor. Its purpose, like any other motor, is to convert electrical energy into mechanical energy. The rotor of the motor moves with the help of pulses generated in the control system. Rotation of the stepper rotor by a given angle causes the controlled object to move by a precisely specified distance.
The rotor consists of two discs with opposite magnetic poles - north and south. When voltage is applied, the rotor is set in motion by the stator winding, or electromagnet. At this point the motor takes one step. The more pairs of poles the rotor has, the smaller this step will be, so the more precise the movement.
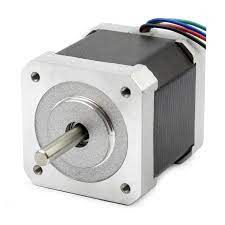
The main difference between a servo motor and a stepper motor is their price. The stepper motor is much cheaper. Nevertheless, it has its disadvantages, which should be taken into account when choosing a device. In stepper motors, there is an open feedback loop, so we do not test whether the motor actually turned by a set value - we only set the number of steps. As a result, during dynamic acceleration or high speeds, the motor tends to lose steps. This translates into lower precision. We should not choose a stepper motor for tasks with high repeatability, implying high precision.